Why Quality Inspection Matters for Office Supplies and Stationery
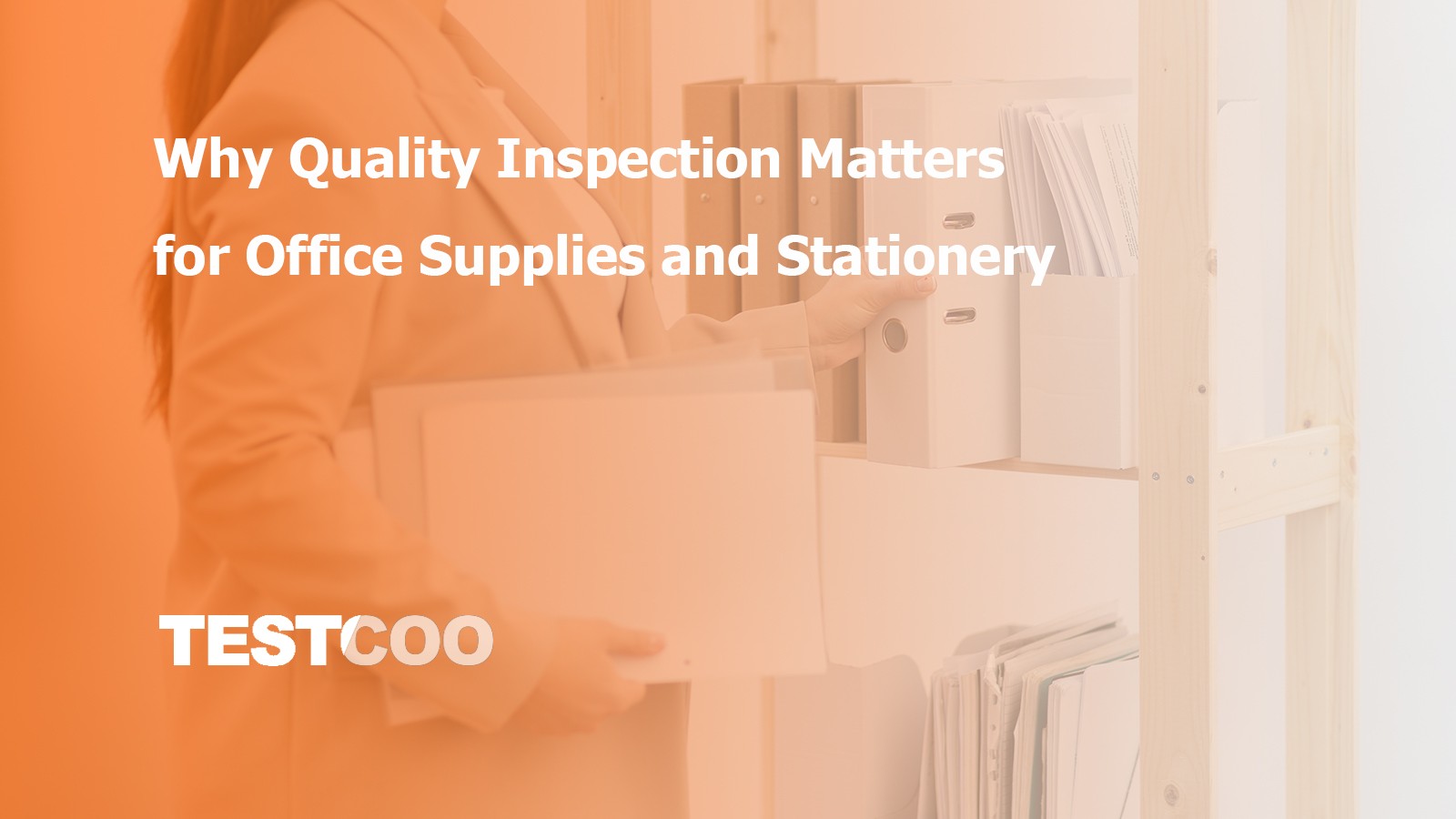
The Significance of Quality Inspection for Office Supplies and Stationery
In the daily operations of any office or educational institution, office supplies and stationery are the unsung heroes that keep things running smoothly. From pens and paper to file folders and printers, these items are essential for productivity, communication, and organization. However, the quality of these seemingly mundane items can have a profound impact on our work and study environments. This is where quality inspection comes into play, and its significance cannot be overstated.
- Ensuring User Safety and Health
The safety of users should always be a top priority when it comes to office supplies and stationery. Poor-quality products can pose serious risks. For example, pens with lead-based inks or stationery items made from toxic materials can be harmful if they come into contact with the skin or are accidentally ingested. In schools, young students may be more vulnerable to such risks. Quality inspection helps to identify and eliminate these potentially dangerous products from the market. By adhering to strict safety standards during the inspection process, manufacturers and suppliers can ensure that the items reaching consumers are free from harmful substances, thus safeguarding the well-being of everyone who uses them.
- Enhancing Productivity in the Workplace
High quality office supplies contribute directly to increased productivity. A smooth-writing pen that doesn't skip or smear allows employees to take notes quickly and clearly during meetings. Reliable printers that produce sharp, smudge-free documents save time and frustration. On the other hand, low-quality supplies can be a constant source of annoyance. A stapler that jams frequently or a printer cartridge that runs out prematurely can disrupt the workflow and cause unnecessary delays. Quality inspection ensures that products meet performance standards, so workers can focus on their tasks without being interrupted by faulty office equipment or subpar stationery.
- Cost-Efficiency in the Long Run
Investing in quality-inspected office supplies may seem more expensive initially, but it can lead to significant cost savings over time. Quality products tend to have a longer lifespan. For instance, a durable file cabinet will last for years, reducing the need for frequent replacements. In contrast, cheap, poorly made cabinets may break easily, forcing businesses to spend more money on new ones in the long term. Moreover, high quality office equipment like copiers and printers that have passed quality inspections are less likely to break down, minimizing costly repair bills and downtime. Quality inspection, therefore, helps organizations make more cost-effective purchasing decisions.
- Maintaining a Professional Image
In a corporate setting, the appearance of office materials can reflect the company's professionalism. High quality stationery with sharp printing and sturdy materials gives a positive impression to clients and partners. A branded notebook with a sleek cover and smooth pages shows that the company pays attention to detail. Conversely, low-quality, flimsy stationery can create a negative perception. Quality inspection ensures that office supplies and stationery uphold the standards that project a professional image, which is crucial for business success.
Key Quality Inspection Standards
- Material Standards
Office supplies and stationery are made from a variety of materials, each with its own set of quality standards.
Paper: For paper products such as copy paper, notebooks, and envelopes, several key parameters are considered. Grammage (weight per unit area) is crucial. For example, standard copy paper usually has a grammage of 70-80 grams per square meter. A higher grammage generally indicates thicker and more durable paper, which is suitable for important documents or double-sided printing. Whiteness is another important factor. High quality paper typically has a whiteness of around 80-90%. A whiter paper provides a better contrast for printing and writing, making text and images more vivid. However, papers with excessive whiteness, especially those achieved through the use of fluorescent brighteners, may be harmful to the eyes. Additionally, the smoothness of paper affects the printing and writing experience. Smooth paper allows for better ink absorption, resulting in sharp and clear text and images.
Plastic: Plastics are widely used in items like pen bodies, file folders, and storage boxes. The type of plastic matters. For instance, polypropylene (PP) is often used for its good chemical resistance, heat resistance, and rigidity. It should be free from impurities and have a consistent color and texture. The plastic should also have sufficient strength to withstand normal use without cracking or breaking easily. In the case of pen bodies, the plastic should be comfortable to hold and have a good grip. For plastic-made storage containers, they should be airtight and leakproof if required.
Metal: Metal is used in products such as staplers, paper clips, and some high-end pen nibs. Stainless steel is a popular choice for its corrosion resistance. For example, the blades of scissors or the parts of a stapler that come into contact with paper should be made of high-quality metal to ensure smooth operation and long-lasting performance. The metal should have the appropriate hardness; too soft a metal may deform easily, while too hard a metal may be brittle. In the case of pen nibs, the metal should be smooth enough to allow for a consistent ink flow during writing.
- Safety Standards
Safety is a paramount concern when it comes to office supplies and stationery, and there are two main aspects to consider: chemical and physical safety.
Chemical Safety: Many office supplies contain chemical substances, such as the glue in adhesives, the ink in pens, and the coatings on papers. These substances must meet strict safety standards. For example, in adhesives, the content of harmful substances like formaldehyde and volatile organic compounds (VOCs) should be minimized. High levels of formaldehyde can cause respiratory problems, eye irritation, and allergic reactions. Inks in pens should not contain heavy metals such as lead, mercury, or cadmium above the permitted limits. These heavy metals can be toxic if ingested or absorbed through the skin, especially in the case of children who may put pens in their mouths. Additionally, the solvents used in markers and highlighters should be nontoxic and have low volatility to prevent inhalation hazards.
Physical Safety: The physical design of office supplies and stationery should also ensure user safety. Sharp edges and points are a major concern. For example, the edges of scissors and knives should be designed in a way that reduces the risk of cuts. In the case of children's stationery, there should be no small parts that can be easily detached and swallowed, as this can pose a choking hazard. Pens should have secure caps to prevent them from coming off accidentally. Some pens are designed with ventilation holes in the cap to reduce the risk of suffocation if a child accidentally swallows the cap.
Read more: https://www.osha.gov/sic-manual/5112
- Functionality Standards
The functionality of office supplies and stationery is directly related to their usability and performance.
For writing instruments: A good-quality pen, whether it's a ballpoint pen, gel pen, or fountain pen, should have a smooth writing experience. The ink flow should be consistent, without skipping, blotting, or bleeding through the paper. For example, a gel pen should be able to write at least a certain number of meters continuously without any issues. Mechanical pencils should have a smooth lead-advancing mechanism, and the lead should not break easily. The erasers on pencils or as separate products should be effective in removing marks without damaging the paper.
For printing and copying supplies, printer cartridges are a key component. A standard ink cartridge for an inkjet printer should be able to print a specified number of pages, usually in the range of hundreds to thousands of pages, depending on the cartridge size and the printer model. The printed text and images should be clear, with accurate colors and sharp edges. Toner cartridges for laser printers should also meet similar performance standards, producing high-quality prints with good toner adhesion to the paper. Copiers should be able to reproduce documents accurately, maintaining the original text size, color, and clarity.
For storage and organization supplies, file folders should be sturdy enough to hold documents without tearing or bending. They should also be easy to label and organize. Storage boxes should have a proper closure mechanism to keep the contents secure. Drawers in filing cabinets should slide smoothly, and the cabinets should be stable to prevent tipping over, especially when fully loaded.
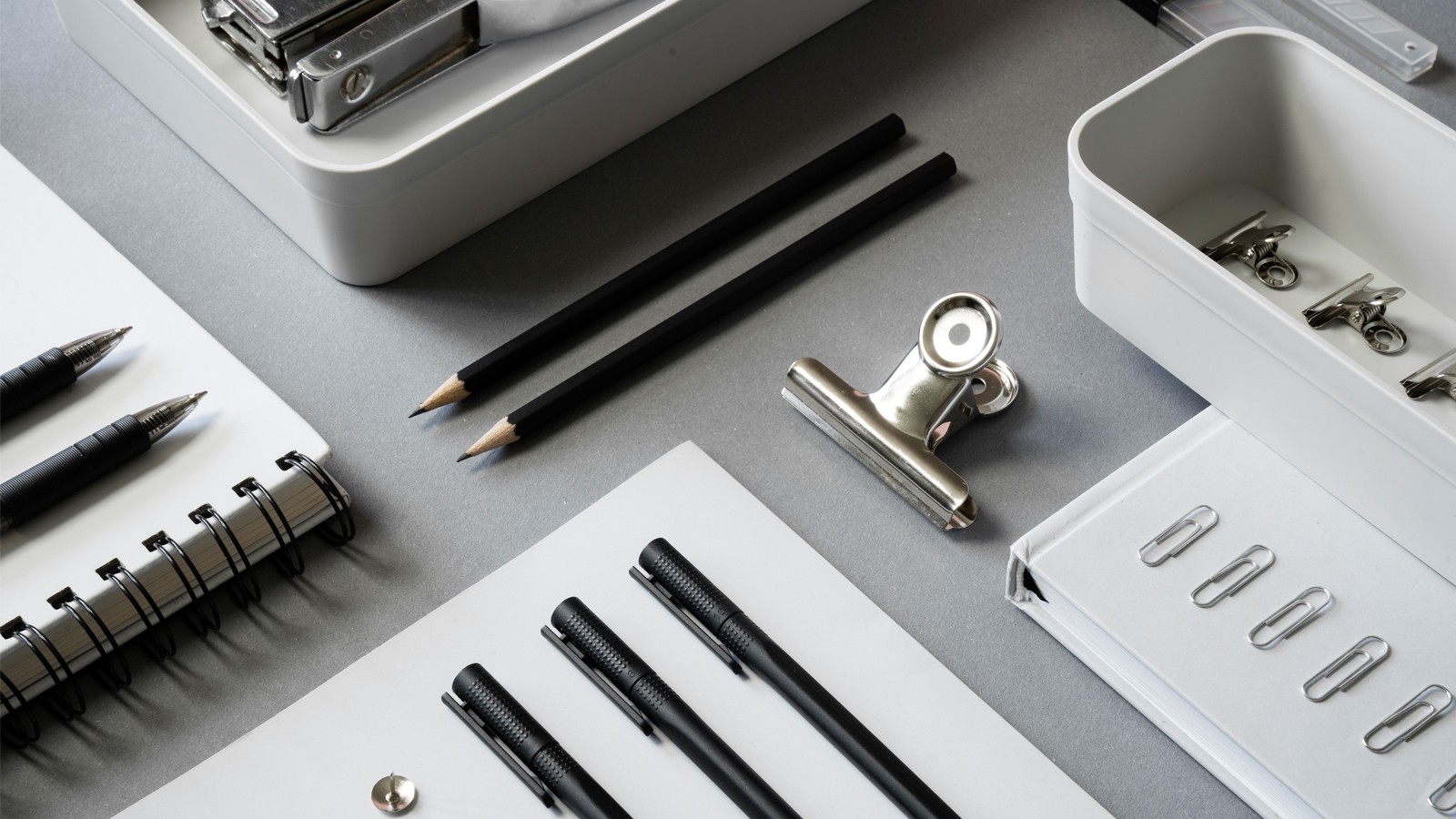
Common Quality Inspection Methods
- Visual Inspection
Visual inspection is the most basic and straightforward method in quality inspection of office supplies and stationery. By using the naked eye, inspectors can quickly assess various aspects of the products.
For the appearance, they check for any obvious defects such as cracks, dents, or warping. For example, when inspecting a plastic file folder, they look for signs of uneven surfaces or small cracks that might develop further during use. The color of the product is also important. In the case of colored papers or pens, the color should be consistent and free from fading or discoloration. If a box of colored markers has markers with inconsistent ink colors, it can affect the user's experience, especially for tasks that require accurate color-coding.
Printing clarity is another crucial factor, especially for products with printed labels or patterns. On notebooks, the printed lines should be clear and evenly spaced. For branded stationery, the logo and brand information printed on the product should be sharp and legible. Blurry or smudged printing not only looks unprofessional but may also indicate poor-quality printing processes, which could potentially affect the durability of the print over time.
- Physical Testing
Physical testing is essential for evaluating the mechanical properties of office supplies and stationery, ensuring they can withstand normal use.
Compression Testing: This is often used for items like file folders, cardboard boxes, and notebooks. For instance, a compression test on a cardboard file box can determine how much weight it can bear before deforming. By placing a gradually increasing load on the box and measuring the point at which it starts to collapse or show significant deformation, manufacturers can ensure that the box can hold the intended number of documents without falling apart.
Tensile Testing: Tensile testing measures the ability of a material to resist pulling forces. In the case of items such as paper clips, binder rings, and the cords on some office accessories, tensile testing is crucial. A paper clip should be able to withstand a certain amount of pulling force without breaking when used to hold papers together. If a paper clip snaps easily under a small tensile force, it is clearly of poor quality.
Wear-Resistance Testing: Many office supplies are subject to repeated use and friction, so wear-resistance testing is vital. For example, the nibs of pens, the wheels on office chairs, and the surfaces of desks are tested for wear resistance. A ballpoint pen nib should be able to write for a long time without excessive wear that would cause the ink flow to become inconsistent. In the case of office chair wheels, they should be able to roll smoothly on different floor surfaces for an extended period without significant wear or damage.
- Chemical Analysis
Chemical analysis is used to detect the chemical composition of office supplies and stationery, ensuring they meet safety and environmental standards.
Elemental Analysis: This involves identifying and quantifying the elements present in a product. For example, using techniques like X-ray fluorescence (XRF), inspectors can detect the presence of heavy metals such as lead, mercury, and cadmium in items like colored pencils, markers, and the coatings on some office equipment. High levels of these heavy metals can be extremely harmful, especially if they come into contact with the skin or are ingested, so strict limits are set to ensure user safety.
Organic Compound Analysis: Methods such as gas chromatography-mass spectrometry (GC-MS) are used to analyze the organic compounds in products. Inks, adhesives, and the plastics used in stationery often contain various organic substances. For example, in the case of adhesives, GC-MS can detect the presence of volatile organic compounds (VOCs) such as formaldehyde. High levels of VOCs can cause respiratory problems and other health issues, so it is important to ensure that these compounds are within safe limits.
Read more about organic compound characterization and quantification here.
Safety Standard Compliance: Chemical analysis results are compared against international and national safety standards. For example, in the European Union, the Restriction of Hazardous Substances (RoHS) directive sets limits on the use of certain hazardous substances in electrical and electronic equipment, which can also be relevant for some office supplies with electronic components. In the United States, the Consumer Product Safety Improvement Act (CPSIA) has strict regulations regarding the lead and phthalate content in children's products, including some children-friendly stationery. By ensuring that office supplies and stationery meet these standards through chemical analysis, manufacturers can guarantee the safety of their users.
Check more important info about CPSIA.
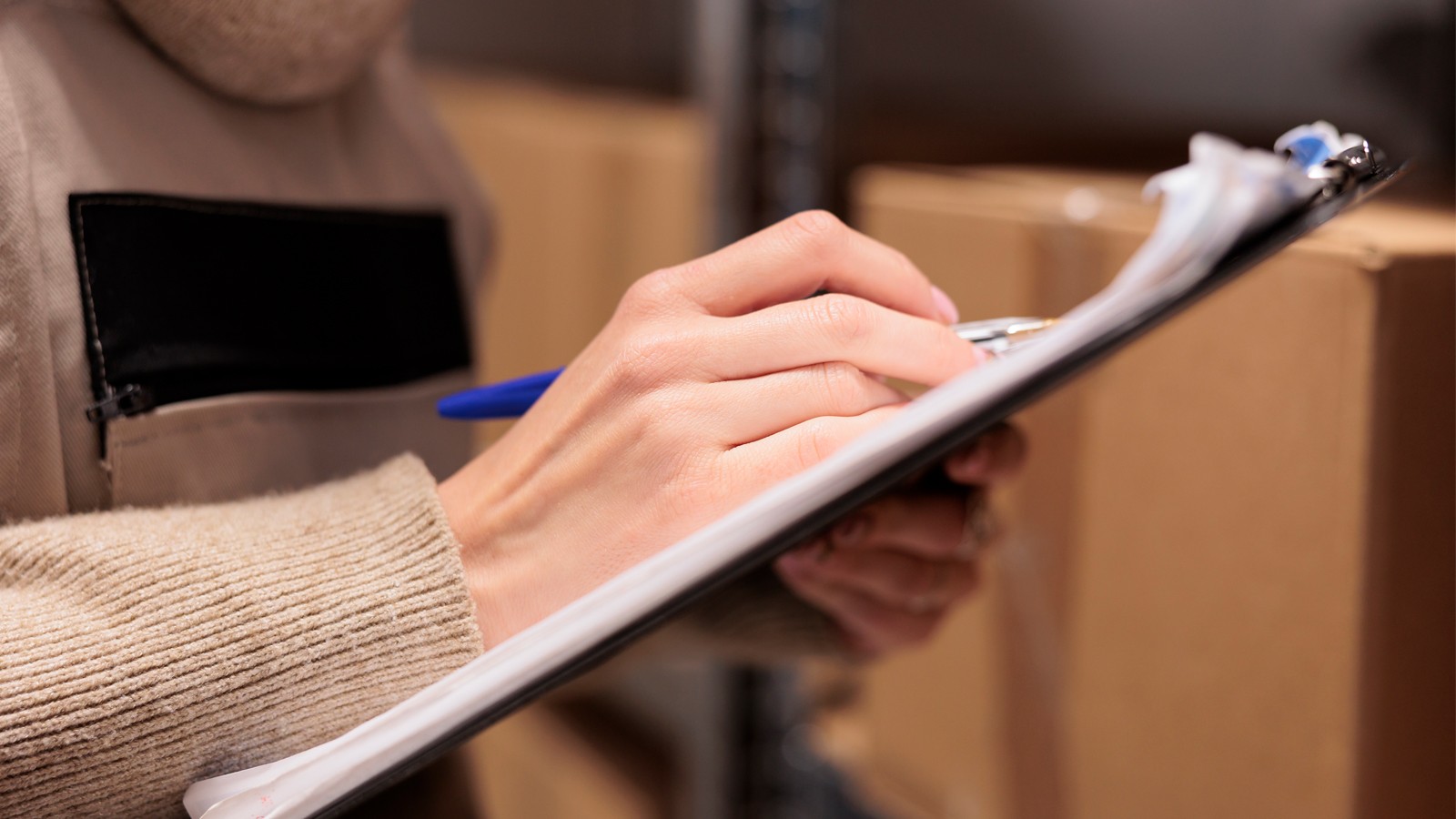
The Consequences of Ignoring Quality Inspection
- Impact on Work Efficiency
Low-quality office supplies and stationery can have a significant negative impact on work efficiency. Consider a simple pen as an example. A pen with a faulty ink cartridge or a ballpoint that doesn't roll smoothly can cause frequent interruptions during note-taking or document-writing. Workers may have to stop what they are doing to shake the pen, replace the cartridge, or search for a new one. This not only wastes time but also breaks the train of thought. In a busy office environment, these small interruptions can add up over time. For instance, if an employee spends just 5 minutes a day dealing with issues related to a poor-quality pen, in a month (assuming a 20-working-day month), that's 100 minutes, or nearly 2 hours, of lost productivity.
Similarly, paper quality matters. When using low-quality paper that is too thin or has poor ink-absorption properties, ink can bleed through the pages. This makes double-sided printing impossible and can make the text on the back side of the page illegible. In a printing-intensive office, such as a marketing department that frequently prints brochures or a law firm that prints legal documents, this can lead to a high rate of reprinting. Each reprint requires additional time for the printer to warm up, load the paper, and produce the new copy. It also increases the waiting time for employees who are relying on those documents for their work.
- Health Risks
The use of office supplies and stationery that contain harmful substances can pose serious health risks to users. Many inexpensive or unregulated products may contain high levels of toxic chemicals. For example, some colored markers and highlighters may have inks that contain volatile organic compounds (VOCs) such as xylene and toluene. Prolonged exposure to these substances can cause respiratory problems, including coughing, wheezing, and shortness of breath. In enclosed office spaces with poor ventilation, the concentration of these VOCs can build up over time, affecting the health of all employees in the area.
Children are especially vulnerable when it comes to harmful stationery. Some cheap plastic-made pencil cases or erasers may contain phthalates, which are known endocrine-disrupting chemicals. If children put these items in their mouths, as they often do, they can ingest these harmful substances. Long-term exposure to phthalates has been linked to developmental and reproductive problems, including reduced fertility and abnormal sexual development in later life. Even in an adult-only office environment, the presence of harmful substances in office supplies like adhesives that release formaldehyde can cause eye irritation, headaches, and allergic reactions over time.
- Cost Increase
Ignoring quality inspection of office supplies and stationery can lead to significant cost increases for businesses and individuals. When office products are of poor quality, they need to be replaced more frequently. Take printer cartridges as an example. A low-quality ink cartridge may run out of ink much faster than a high-quality one, or it may produce poor-quality prints that require reprinting. This means that businesses have to spend more money on purchasing replacement cartridges more often. If a company spends $50 a month on printer cartridges for a single printer, but due to using low-quality cartridges, they have to replace them twice as often, the monthly cost for that one printer alone jumps to $100.
In addition to the cost of replacement products, there are also indirect costs associated with low-quality office supplies. For example, if a stapler constantly jams, employees may waste time trying to fix it or find a new one. This lost productivity has an associated cost. If an employee's hourly wage is $20 and they spend 15 minutes a day dealing with a faulty stapler, that's $5 worth of lost productivity per day. Over a month, this amounts to $100 (assuming 20 working days). These indirect costs can quickly add up and have a substantial impact on the overall budget of an organization.
How Testcoo Can Help
When it comes to ensuring the quality of office supplies and stationery, Testcoo, as a leading professional third-party inspection company, offers a comprehensive range of services.
Testcoo provides meticulous product inspection services. Whether it's a batch of newly produced pens, boxes of copy paper, or high-tech office equipment, our team of experienced inspectors can conduct in-depth inspections. We use a combination of visual inspection, physical testing, and chemical analysis methods as described earlier. For example, during the inspection of pens, we will check the smoothness of the writing experience, the quality of the ink, and the durability of the pen body, ensuring that each pen meets high-quality standards. In the case of paper products, we will verify parameters such as grammage, whiteness, and smoothness to ensure optimal printing and writing performance.
In addition to product inspection, Testcoo also offers supplier audit services. We can visit the factories of office supply and stationery suppliers to assess their production processes, quality management systems, and compliance with safety and environmental standards. By evaluating the supplier's manufacturing capacity, raw material sourcing, and production environment, Testcoo can help you determine the reliability of the supplier. This not only helps in ensuring the quality of the products but also in building long-term and stable business relationships.
If you want to ensure that the office supplies and stationery you use or sell are of high quality, safe, and meet all relevant standards, don't hesitate to turn to Testcoo. Our services can provide you with the peace of mind you need to focus on your core business, knowing that the quality of your office products is in good hands.
Free Sample Report Performance Quality Control
Download a sample report to keep control of your supply chain!
Featured Articles
- AQL Table | How to Read It
- TOP 10 Common Defects in Garments Quality Inspection
- Product Packaging and Shipment Label requirements for Amazon FBA
- What Is ASTM-F2413-18? Protective Footwear Standard
- How to Conduct Third-Party Quality Control Inspections for Electric Scooters
- SMETA Audit-What is SMETA Audit?
- TESTCOO Supplier Verification/Certification Service SLCP, Higg FEM, GRS, GOTS
- Quality Control Inspection Company in China
- What is Quality Inspection? A Complete Guide
- Guidelines for Product Inspection in India
Category
- Production Inspection Service
- Factory Audit
- Softline Inspection
- Hardline Inspection
- Electrics Inspection
- Certification
- Checklist
- Manufacturers
- Quality Assurance Basics
- Products Recall
- AQL
- Guidence and Standard
- News
- Supplier Management
- Amazon
- Protective Equipment
- e-commerce quality control
- Indian Manufacturing
- Soft Goods Quality Control
- Supply Chain Management
- Supply Chain Resilience
- E-Commerce Quality Control
- ISO 2859
- Supply Chain Optimization
- Garment Industry
- Higg Index