Quality Check in Manufacturing: A Step-by-Step Guide for Global Buyers
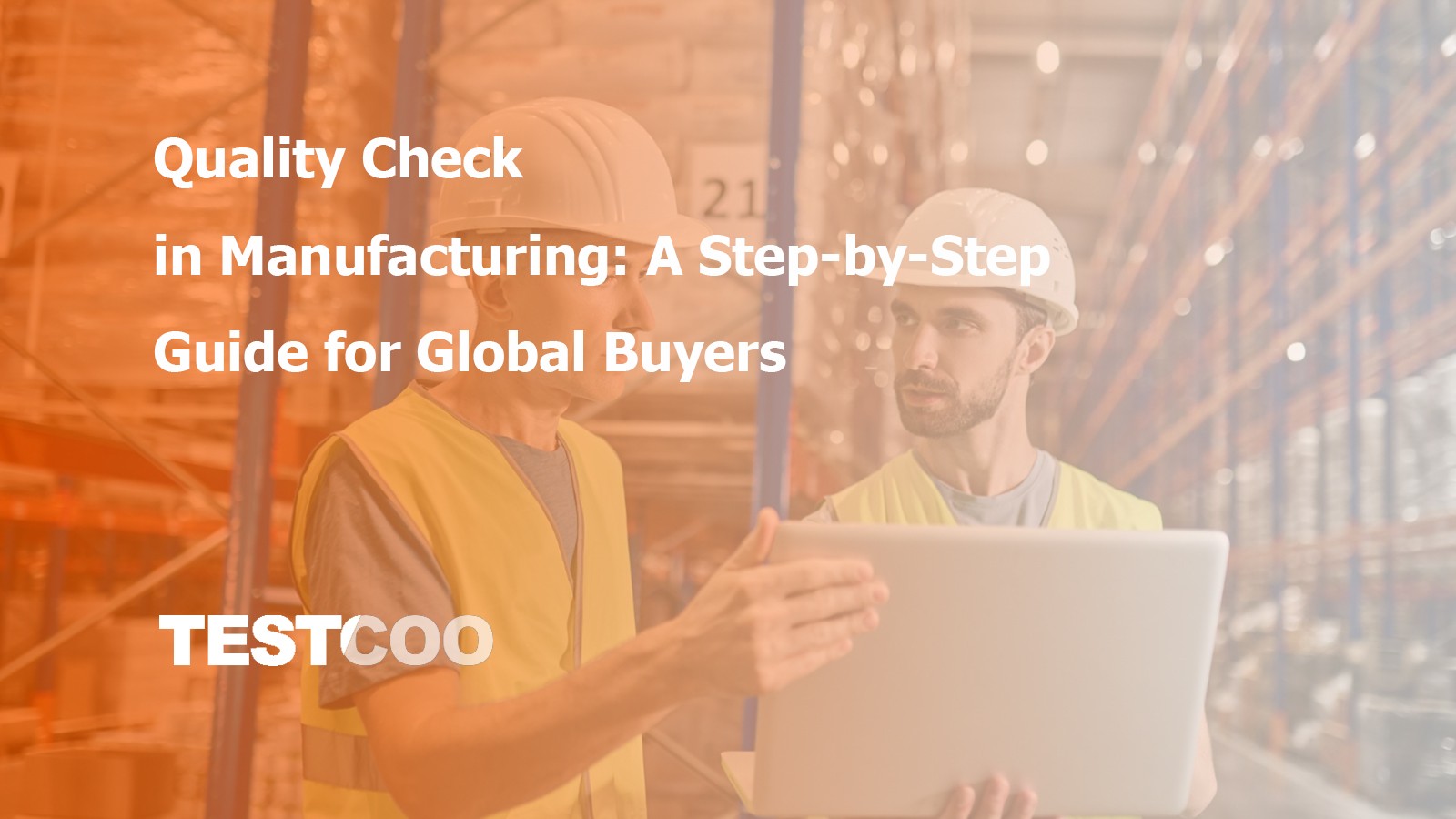
In today’s competitive global marketplace, one defective batch can cost a business not only money but its hard-earned reputation. That’s why quality checks in manufacturing are vital for buyers sourcing from overseas suppliers. Whether you’re an established brand owner, a sourcing agent, or an importer working with manufacturers in Asia or elsewhere, knowing how quality checks work and implementing them well is the only way to ensure consistent product standards.
In this practical guide, we’ll break down what a quality check in manufacturing actually involves, why it’s non-negotiable and how global buyers can implement a robust inspection process step by step.
What Does “Quality Check in Manufacturing” Mean?
At its core, a quality check (or quality inspection) is a systematic process to verify that the products being made meet agreed-upon specifications, standards and requirements. This process includes inspecting raw materials, monitoring production, sampling finished goods and ensuring packaging and labeling are correct.
The ultimate goal is to detect defects or non-conformities early when they are cheaper and easier to fix rather than after the goods have shipped.
Why Quality Checks Matter for Global Buyers
Outsourcing production overseas brings major advantages in terms of cost, scale and speed. But it also brings risks:
- Suppliers might substitute materials.
- Workmanship may not meet your required standards.
- Deadlines might be missed.
- Packaging may not comply with importing country rules.
Without regular quality checks, buyers expose themselves to costly surprises like customer returns, penalties, or entire shipments stuck at customs. An effective quality check in manufacturing acts as a safety net making sure you get what you paid for.
Key Benefits of a Strong Quality Check System
A strong quality check system is the silent backbone of any successful manufacturing operation. Imagine a company that once struggled with customer complaints, high return rates and wasted resources due to unnoticed defects slipping through production lines. By investing in a robust quality check framework from raw material inspection to final product audits, this company turned its reputation around.
Each product is now checked at every critical stage, minimizing errors and ensuring only compliant goods reach the customer. This system not only prevents costly recalls but also boosts customer trust and brand loyalty. Workers feel empowered knowing clear standards guide their work, while managers gain valuable data to improve processes and reduce waste.
Over time, this culture of quality saves money, protects brand image and opens doors to new markets with stricter compliance standards. In industries where one defect can ruin a contract, a strong quality check system becomes the competitive edge.
In short, quality checks are not just a box to tick, they are a strategic investment that fuels efficiency, safeguards reputation and builds a foundation for long-term growth in a demanding global market.
- Reduce Defects: Identify problems early.
- Protect Your Brand: Deliver consistent quality that builds trust.
- Lower Costs: Catching mistakes upstream costs far less than recalls.
- Comply with Regulations: Ensure your goods meet legal and safety requirements.
- Strengthen Supplier Accountability: Inspections hold factories to their promises.
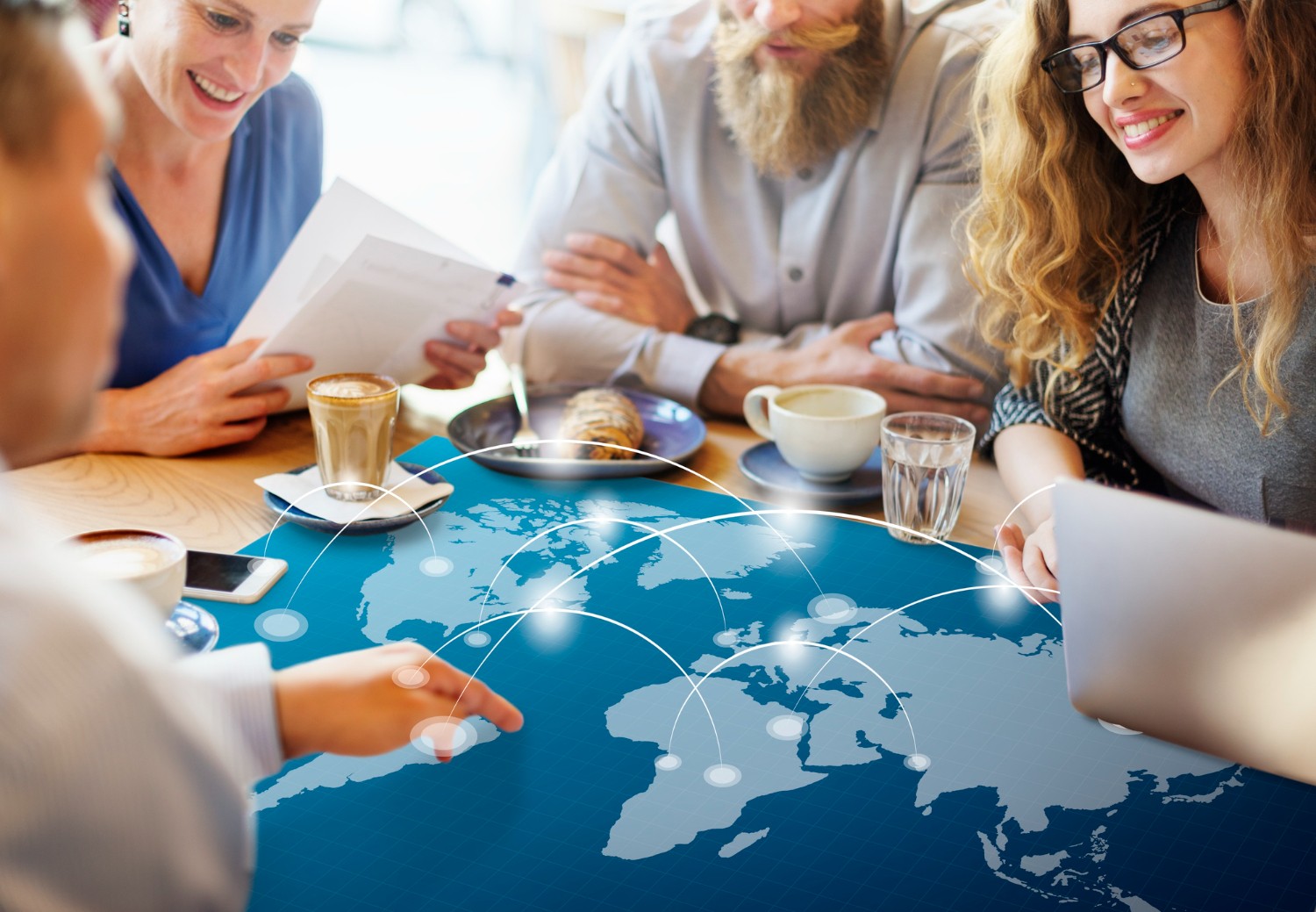
The 5 Stages of Quality Checks in Manufacturing
A single “final inspection” is not enough. A robust quality check process covers the entire production lifecycle:
- Initial Production Check (IPC)
- During Production Inspection (DUPRO) / In-Process Inspection
- Final Random Inspection (FRI) / Pre-Shipment Inspection
- Loading Supervision (LS)
- Laboratory Testing (when needed)
Let’s break each one down.
1. Initial Production Check (IPC)
This inspection happens before production begins. It focuses on:
- Verifying raw materials and components: Are they the correct type, grade and quantity?
- Checking tooling, machinery and processes: Are they suitable for your specifications?
- Reviewing production schedules and capacity: Can the factory meet your deadline?
Why it matters: Detecting problems before production avoids costly rework later.
Example: Imagine you’re sourcing organic cotton T-shirts. A PPI could confirm the fabric is genuinely organic-certified and dyed to your approved colors before cutting starts.
2. During Production Inspection (DUPRO)
This check happens when 20%–50% of production is completed. Inspectors:
- Check samples from the production line for defects.
- Verify workmanship, measurements and finishing details.
- Monitor production speed vs. the delivery schedule.
- Provide early warnings if the defect rate is rising.
Why it matters: Catching issues mid-production lets the factory correct course before the entire batch is flawed.
Example: If stitching is uneven or print alignment is off, the factory can adjust immediately, saving time and materials.
3. Final Random Inspection (FRI)
This is the most common type of quality check in manufacturing, a random sample is checked when at least 80% of goods are packed.
Inspectors look at:
- Product appearance, functionality, dimensions
- Workmanship and finishing
- Labeling, barcodes and packaging
- Compliance with buyer specifications
- Quantity and packing lists
This check uses AQL (Acceptable Quality Limit) sampling methods to statistically assess whether the lot meets the agreed defect tolerance.
Why it matters: The FRI is your last line of defense before shipment.
Example: For electronics, a final inspection would check power-up tests, buttons, displays and safety labels.
4. Loading Supervision (LS)
This inspection ensures that:
- The right products and quantities are loaded.
- Cartons are in good condition.
- Sealing and container cleanliness meet standards.
- The container is sealed properly with a recorded seal number.
Why it matters: Prevents your goods from being swapped or damaged during loading.
Example: For fragile glassware, a CLC can confirm that cartons are handled carefully and stowed securely to minimize breakage in transit.
5. Laboratory Testing (When Needed)
Certain products especially textiles, toys, electronics, or food-contact items may need lab tests for chemical safety, performance, or compliance.
Examples include:
- Checking fabric shrinkage, colorfastness, or harmful substances.
- Verifying electrical safety for consumer electronics.
- Ensuring toys comply with child safety standards (EN71, ASTM F963).
Why it matters: Some issues can’t be spotted visually, lab testing provides scientific verification.
Read more: The Importance of Third-Party Quality Inspection: Ensuring Excellence in Every Step
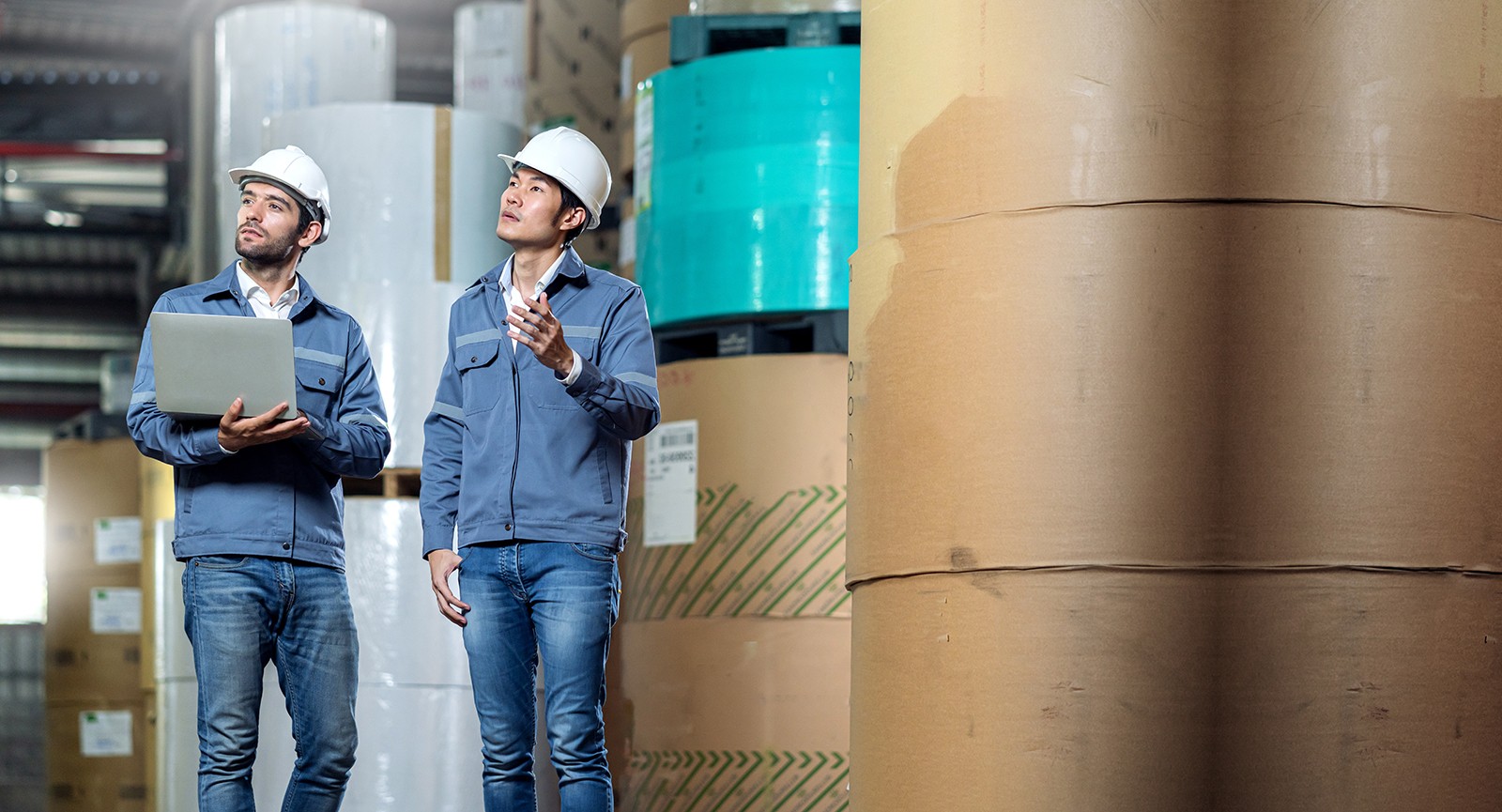
How AQL Sampling Works
A big part of final inspections is AQL (Acceptable Quality Limit). It’s a statistical method for defining how many defective units are acceptable in a sample.
How it works:
- You choose an AQL level (like 2.5% for major defects, 4.0% for minor).
- Inspectors take a random sample based on the lot size and check each unit.
- If defects exceed the AQL, the batch may be rejected or reworked.
Using AQL properly helps buyers balance inspection cost with risk tolerance.
Read more about AQL Sampling Inspection - How to Read Tables and Design a QC Plan
Best Practices for Global Buyers
How can you make sure your quality check in manufacturing works in the real world?
1. Define clear specifications
A good inspection starts with clear, measurable specs:
- Approved samples
- Technical drawings
- Material lists
- Packaging artwork
- Label requirements
Leave no room for assumptions.
2. Work with trusted third-party inspectors
Partner with experienced inspection companies like Testcoo, they bring local expertise, unbiased reporting and faster response times.
3. Communicate with your supplier
Share inspection criteria upfront. Make it clear that passing inspections is a non-negotiable part of doing business with you.
4. Be consistent
Do not skip inspections to save money, that’s when problems slip through.
5. Take action on results
If defects are found, work with your supplier on corrective actions. Hold them accountable for replacements or rework if needed.
Technology & Trends in Quality Checks
Modern quality checks are no longer only clipboards and checklists. Leading buyers and inspectors are using:
- Real-time reporting tools: Instant updates with photos and videos.
- Remote inspections: Live video checks when travel is restricted.
- Data analytics: Aggregating defect trends to spot recurring problems.
- AI-powered inspections: Early days, but machine learning is starting to help detect defects faster.
Staying ahead with digital tools helps you manage quality more proactively.
Read more: Unleashing the Power of Tech in QC & Inspection: A Deep Dive with Testcoo
How Testcoo Can Help
At Testcoo, we help global buyers like you ensure consistent product quality from thousands of factories worldwide. Our experienced inspectors understand local cultures, factory realities and global compliance standards.
We offer:
- Pre-production, in-line, final and loading inspections.
- Lab testing partnerships for specialized needs.
- Digital reports with real-time results.
- Flexible booking to match tight production schedules.
With Testcoo, you can sleep better knowing that your products are checked at every step, not just when they arrive at your warehouse.
A robust quality check in manufacturing process is not a luxury, it’s an essential part of modern global supply chains. When done right, it protects your business, your brand and your bottom line.
Whether you’re sourcing textiles in India, electronics in China, or toys in Southeast Asia, following a clear step-by-step inspection plan and working with a trusted partner like Testcoo will help you deliver quality that your customers can rely on.
Ready to make quality your competitive edge?
👉 Contact Testcoo to learn how we can help you build stronger supplier relationships, minimize risks and grow your business with confidence.
Free Sample Report Performance Quality Control
Download a sample report to keep control of your supply chain!
Featured Articles
- AQL Table | How to Read It
- TOP 10 Common Defects in Garments Quality Inspection
- Product Packaging and Shipment Label requirements for Amazon FBA
- What Is ASTM-F2413-18? Protective Footwear Standard
- How to Conduct Third-Party Quality Control Inspections for Electric Scooters
- SMETA Audit-What is SMETA Audit?
- TESTCOO Supplier Verification/Certification Service SLCP, Higg FEM, GRS, GOTS
- Quality Control Inspection Company in China
- What is Quality Inspection? A Complete Guide
- Guidelines for Product Inspection in India
Category
- Production Inspection Service
- Factory Audit
- Softline Inspection
- Hardline Inspection
- Electrics Inspection
- Certification
- Checklist
- Manufacturers
- Quality Assurance Basics
- Products Recall
- AQL
- Guidence and Standard
- News
- Supplier Management
- Amazon
- Protective Equipment
- e-commerce quality control
- Indian Manufacturing
- Soft Goods Quality Control
- Supply Chain Management
- Supply Chain Resilience
- E-Commerce Quality Control
- ISO 2859
- Supply Chain Optimization
- Garment Industry
- Higg Index