Fabric Inspection
See how Testcoo fabric inspection solutions can help mitigate risks related to incidents and faulty product performance.
Fabric Inspection in Textile and Apparel Manufacturing
Any garment or piece of clothing is valued or purchased by measuring the quality of the fabric. Whether it is the buyer, customer, or wholesaler of garments today all look for quality and standard fabrics.
Damage in fabrics can bring the cost down by 45 to 65 percent. Hence fabric inspection plays a significant role in the process of making garments. The inspection is usually carried out before the production of garments begins and checks the quality of the fabric, sewing thread, and the trims and accessories.
Fabric inspection is performed in a different method from other textile. It uses a numerical designation for the grading of fabrics from a visual inspection. Normally, it’s also called fabric inspection 4 point or 10 point system. 4 point system is taken a priority to be used. 10 point system is only to be used once it is requested.
CONTENTS
Chapter1: Why is fabric inspection so important?
A fabric inspection can prevent defects in the final product but there are several other reasons it is a crucial element for any factory.
Whether it is a reduction in productivity or increased overheads, garment brands/suppliers can face production challenges from defective fabric such as:
-Inconsistencies in the cut table width will impact their fabric consumption/wastage.
-Different color shading among rolls or within the same roll impacts product quality and requires special management during the cutting/sewing/packing and other production steps to segregate by color shades.
-High defect rates in the fabric ( such as stains/holes etc.) will impact the consumption per garment and increase the risk of defects found in the garment.
Chapter2: What is the standard used in fabric inspection?
1. Sampling and Sample Size
-Sampling for the inspection of bulk fabric generally does not follow the same parameters as the ones for garments.
Typical sampling parameters for Fabrics are listed below.
Lot size | Sample size |
<500 yards / meters | Full sample |
> 500 yards / meters | (Square root of lot size) X 10 |
-The required Sample Size will be selected randomly from the rolls present in the shipment. The entire length of each roll or piece selected will be inspected until the required Sample is completed.
-A minimum of 2 roll per color should be selected.
-Usually, one inspection (one sampling) is only to cover the same style of fabric. The same style means the same content of fiber, the same yarn size, the same construction, the same fabric weight, the same cuttable width. Multiple colors of the same style of fabric can be combined into an inspection report.
2. The 4 Point System
Provided as a means of defining defects according to their severity by assigning demerit or penalty points. All types of fabrics, whether grey or finished, knit or woven, can be graded by this system. Visible defects are scored in proportion of the size of the defect.
Defect ( English Units) | Defect Size ( SI Units) | Penalty Points |
Defect≤3 inches | Defect ≤75 mm | 1 |
3 inches | 75 mm | 2 |
6 inches < defect ≤9 inches | 150 mm < defect≤230 mm | 3 |
Defect <9 inches | Defect < 230 mm | 4 |
3. Quality Criteria
01. The whole shipment would be “FAIL” as below:
-If the Penalty points per shipment is over the requirement.
-If the second quality percentage is over 10%.
-The total measured inspected length is less than 1% against the ticket length.
-Any inspected roll’s design / pattern / construction is not conformed to the description on the order or approved sample.
02. The individual roll would be considered as “SECOND QUALITY” and no need to assign penalty points to below defects:
-Shade evaluation: Roll that is outside of the Grey Scale 4-5 against the approved sample
- Shade continuity: Roll that is outside of the Grey Scale 4-5 within one roll
-Pattern size: If the actual difference that 27”/70cm minus actual length counted with same repeats in bulk compared to specific length 27”/70cm is over the tolerance +/- 1%
-Cut table width: Narrow width – no tolerance, any minus than the specified
-Bow / Skew: For Woven: +/- 2% for print or check, +/- 3% for Solid
-Poor selvage : Rolls exhibit a noticeable degree of looseness or tightness along either or both sleeve edges, or ripples, puckers, folds or crease in the b of the fabric that will prevent the fabric from lying flat when being spread in conventional manner.
-Running defect: Running defect is each individual defect with its size over 9”/230mm and shall be counted as 4 penalty points in each yard and the same defects repeat through more than 10 continuous yards /meters (including 10 continuous yards /meters), the individual roll will be considered as “second quality”. No need to assign penalty points for the running defects.
03. The individual roll would be considered as “SECOND QUALITY” and assigned penalty points:
-Splices: Minimum splice length of 30 yards / meters for all fabrics. No rolls shall be accepted containing more than one splice or two joined pieces
-Full width defect: No roll that contains more than four full width defects per one hundred linear yards /meters.
Chapter3: Fabric Inspection Checklists on field test
1. Bow and skew check
The general acceptable tolerance is 3% if no specified from client.
2. Color Shading Check
Check for color shading differences within a dye lot may not vary within a roll/piece (side to side, side center side, or end to end shading) or between rolls/pieces, he shade must match with the approved sample standard(swatch card).
Compare against the same lot product Grey scale 4-5 is general acceptable level if no requirement from client. If color shade is out of acceptable level, the inspected roll will be down grade instead of count into penalty point.
3. Odor and smell check
Should not have irritative smell and odor.
4. Roll length
The roll length is measured by a meter counter. Fabric roll length may be rejected when shorter than 2% compare against ticket length. Penalty point will not be assigned, but will put into conclusion of report. If the total measured length is less than 1% total ticket length, the whole shipment lot may be rejected.
5. Fabric width
Fabric width should be checked 3 times for inspected roll. Beginning, middle and end (minimum 5 yards from beginning and end) Assign 4 points to each linear yard of fabric where the cut table width is less than the minimum specified. The roll will be down grade instead of assign penalty point when the Fabric width of whole roll is less the specification.
6. Fabric Weight Check
GSM per fabric should be recorded in report & check with spec & approved sample. Record in gram per 100 square meter 3 specimens. The general tolerance is +/-3% if no requirement from client
7. Damp and Mildew check
Should not damp or mildew.
8. Color fastness
Should not color stain.
9. Moisture check
Moisture check should be for each roll by a moisture tester, please remark if the moisture more than 12%.
Chapter4: Fabric Inspection Defect Classification
Refer to ASTM D 3990-12: Standard Terminology Relating to Fabric Defects. Typical defects for fabrics are listed below.
DEFECT | DESCRIPTION | ||
Abrasion Mark | Area damaged by friction. | ||
Barre | Band, stripe, streak, or bar characterized by a visible difference in texture, color, or luster of adjoining picks. A repetitive and patterned unevenness of appearance in the course or widthwise direction of a fabric. | ||
Bias (or Skewness) | Wovens: Filling yarns are not square to the warp ends. Knits: Courses are not square to the wales. | ||
Bow | Wovens: Filling yarns lie in an arc across the width of the fabric. Knits: Courses lie in an arc across the width of the fabric. | ||
Broken End | Wovens: Space in warp direction due to broken yarn. | ||
Broken Pick | Wovens: Space in filling direction due to broken yarn. | ||
Bruise | Area damaged by impact or pressure. | ||
Burl Mark | Mark left by removal of slub or extra piece of yarn that has been w into a fabric. | ||
Coarse End | A larger than normal diameter warp end. | ||
Coarse Pick | In woven fabrics, one or more picks of larger diameter the normal filling yarn in the fabric. | ||
Color Stain | The undesired pickup of color by a fabric when 1) immersed in water, dry-cleaning solvent, or similar liquid medium, that contains dyestuffs or coloring material not intended for coloring the fabric, or (2) by direct contact with other dyed material from which co or is transferred by bleeding or sublimation. | ||
Crease Mark | Visible streak in fabric caused by folding | ||
Cut Selvage | Cuts or breaks in the selvage area only | ||
Draw-back | Excess tight and slack areas in the same warp yarn. | ||
Dropped Stitch | Knits: Unknitted stitch. | ||
Dyestain | An area of unintended discoloration uneven absorption of a colorant. | ||
Dye Streak | Irregular streak caused by uneven dye absorption. | ||
End Out | Thin line or space ca by missing warp yarn. | ||
Fabric Pest Hole | Especially for fabric made of natural protein fiber, such as wool, silk, caused by insects whose larvae damage fabrics by producing an enzyme and digesting keratin of natural protein fiber. | ||
Filling Band | In woven fabrics, a visual defect across the width due to a change occurring in the yarn for a large number of picks. (Com are filling bar) | ||
Filling Bar | In woven fabrics, a visual defect across the width which contains a limited number of picks of different appearance than normal. (Compare filling band) | ||
Fine End | a smaller than normal diameter warp end. | ||
Float | In woven fabrics, that portion of a warp or filling yarn that extends unbound over two or more warp or filling In knit fabrics, that portion of a yarn that is not knitted into loops. | ||
Fly | Waste fibers or fuzz unintentionally woven into a fabric. | ||
Hole | In fabric, an imperfection where one or more yarns are sufficiently damaged to create an aperture. | ||
Mispick |
| ||
Misprint |
| ||
Mixed End | Wovens: Warp yarn different in color, size, or type than the rest of the fabric. | ||
Mixed Filling | Wovens: Filling yarn different in color, size, or type than the rest of the fabric. | ||
Pin Hole | Very small hole. | ||
Out of Register (or Misregister) | in printed fabric, colors or patterns not correctly positioned. | ||
Pin Mark | Series of pin holes along the selvage caused by a holding device. | ||
Reed Mark | Crack between groups of warp ends. | ||
Run | Series of dropped stitches. | ||
| Mark or crease caused by sewn seam pressing against adjacent fabric. | ||
| Lengthwise crease near selvage caused by folding or doubling of fabric edge. | ||
Skewness (or Bias) | Wovens: Filling yarns are not square to the warp ends. Knits: Courses are not square to the wales | ||
Slub | Abruptly thickened place in a yarn. | ||
Snag | Yarn or piece of yarn pulled from the surface of a fabric. | ||
Spot | Small discoloration on surface of a fabric. Can be caused by dying, foreign matter (dirt, oil, water) etc. | ||
Stain | Discoloration that penetrates the surface of a fabric. | ||
Streak | Extended narrow stripe, often a single yarn. | ||
Thick Place | Small area of closely spaced and/or thicker diameter yarns when compared to the average construction of the fabric. | ||
Thin Place | Small area of loosely spaced and/or thinner diameter yarns when compared to the average construction of the fabric. | ||
Uneven Dyeing | Cloth which shows variations in shade due either to incorrect dyeing methods or faulty materials. | ||
Warp Streak | Narrow band or stripe running lengthwise | ||
Wrinkle | A short and irregular crease. |
Chapter5: How Testcoo performs an on-site Fabric Inspection
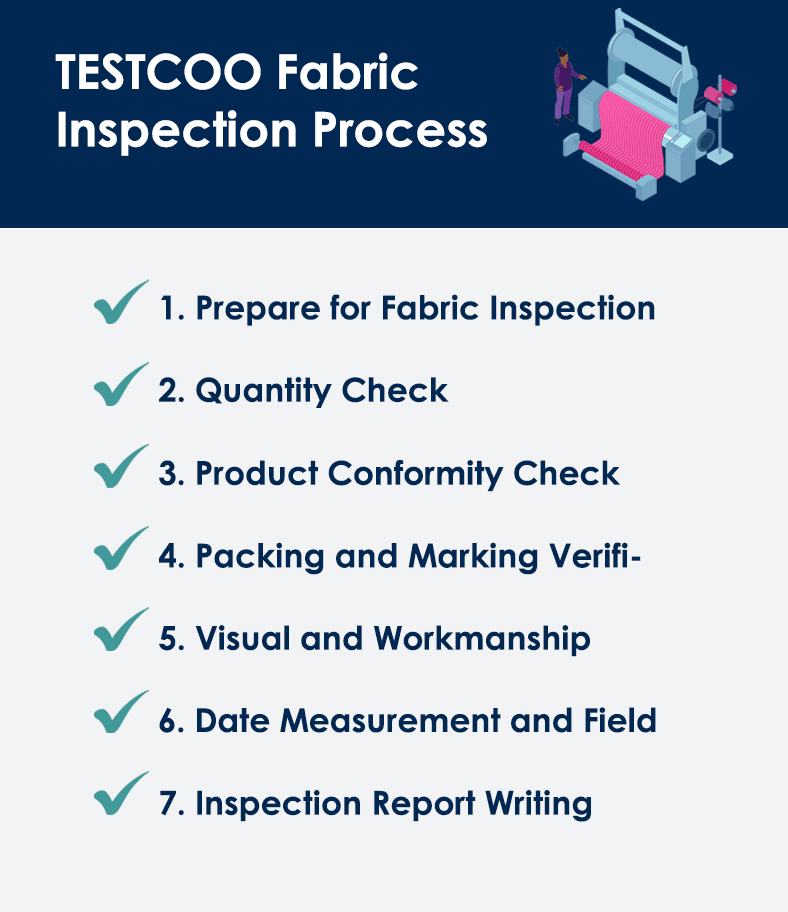
Fabric inspection is an essential step in the garment and textile industry as it ensures that fabrics meet the necessary quality standards and specifications before they are used in manufacturing.
TESTCOO fabric inspection are covering some of the basic steps so you can get practical tips on this, whether you are a merchandiser or a garment supplier.
TESTCOO Fabric Inspection Process
1. Prepare for Fabric Inspection
Before starting the fabric inspection, it is important to make sure that the factory has totally finished the fabric and you have all the necessary tools and equipment. This may include a fabric inspection checklist, a ruler or measuring tape, and a fabric inspection machine that the factory has. Make sure that the area where the inspection is taking place is clean, well-lit, and free of dust or other contaminants.
2. Quantity Check
Check to ensure the actual shipment finished quantity and packed quantity.
3. Product Conformity Check
Inspectors work either with fabric samples provided by clients as the comparison samples or, in the absence of fabric samples from clients, the beginning and end of the roll will be cut for conformity checking against the inspected roll.
Conformity is assessed on
- Colors
- Style
- Elasticity
- Hand feels, etc.
4. Packing and Marking Verification
The identification stickers, shipping marks, packing lists and packing quantity, labeling, and barcode are checked against the requirements and specifications.
5. Visual and Workmanship Check
The color, look and feel, fabric construction, printing defects, appearance, and edge to edge shading are commonly checked during a fabric inspection. Inspection of fabrics not just help in location of defects but also aid in preventing future rejects, achieve greater efficiency, and attend to deliveries in time.
6. Date Measurement and Field Test
Perform all the field tests as fabric inspection checklists.
- -Bow and skew check
- -Color Shading Check
- -Odor and smell check
- -Roll length
- -Fabric width
- -Fabric Weight Check
- -Damp and Mildew check
- -Color fastness
- -Moisture check
7. Inspection Report Writing
Document any defects that were found during the inspection and take pictures if necessary. After inspection, prepare a detailed report of the findings, including any defects found, measurements taken, and any other relevant information. Share the report with the supplier or other relevant parties, including the production team, so that they can take appropriate action to correct any issues that were identified during the inspection.
Fabric Inspection Report
A detailed report of the findings, including any defects found, measurements taken, and any other relevant information.
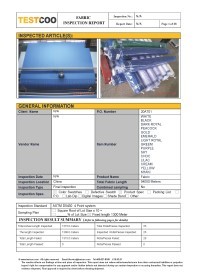
Conclusion
It is the responsibility of both the textile supplier and garment manufacturer to inspect all textiles to ensure their compliance with the buyer standard. Fabric inspection is a critical step in the textile manufacturing process that helps to ensure that the fabric meets the required standards before it is used to make garments or other products.
FAQs
1. What is the system used in fabric inspection?
There are several grading systems adopted for fabric inspection such as the 10-point system and the Dallas system. Among all, the 4-point system has become the most commonly adopted system for fabric inspection.
The 4-point system works on a penalty point basis and as its name has probably suggested, points are deducted from 1 to 4, with 4 points being the highest deduction for major defects.
2. What sample size is used?
Before doing the inspection the sample must be decided. Fabric coming in from the mill may be in large quantities of rolls and, as with many incoming product, material, or component inspections, it’s often unrealistic to inspect 100%. That’s why a representative sample is taken at random.
The AQL sample size is usually 10% of the order quantity, especially for orders above 1000 m or yd, although for smaller order quantities the entire batch may be checked.
3. What your fabric inspection may find?
- Issues that may commonly be found are:
- -Discrepancies in color or texture between the different batches or rolls of fabrics
- -Rolls with varying widths that would lead to wastage once cut
- -Fabric that has been provided with defects , again leading to wastage or defective products
- -Incorrect weight of fabric provided in the case of a fabric where different weights are available
- -Fabric with a defective design or print or even a totally wrong one
- -Incorrect yarn count, composition, density of fabric provided (this can only be measured in a testing lab, and in many factories an inspector does not have the capability to do so)
- -Packing and labeling problems
4. How does fabric pass or fail?
Firstly, the customer needs to determine how many defects are acceptable per one hundred square yards or meters of fabric. The number will vary depending on fabric cost and the final value of apparel or textiles to be made. Cheaper clothing, for example, may result in a higher tolerance for defects in the raw fabrics being used.
5. What will be the arrangement for defective fabric?
Depending on the seriousness of the defects, fabric might be discarded and a replacement will be required. For instance, different color shading among rolls requires special management during cutting to segregate by color shades.
In some other cases, defects of fabric can be avoided during the cut & sew phase as defects are marked by defect stickers clearly.
6. How much fabric can be checked in a man-day?
In 1 man-day, we can check 1200 meters of fabric if the factory has the proper fabric inspection machine.
If you need assistance inspecting fabric, get in touch with us and let us know more about the project.
Related Articles
Read MoreFree Sample Report Performance Quality Control
Download a sample report to keep control of your supply chain!