Top 30 Third-Party Inspection companies in China You can Trust

Buyers always suffer huge losses due to quality problems with goods purchased overseas. An obvious way to control the problem is to find an inspection company in China to check the quality before shipping.
An effective way to solve this issue is to find a Chinese inspection company to conduct a pre-shipment inspection. A professional third-party inspection company can effectively help you reduce risks, avoid shipping delays, reduce return rates and so on.
With numerous inspection companies in China, how do you choose the right one for your business? Here is a comprehensive guide covering costs, types of inspections, and tips for working effectively with inspection companies.
How much does an inspection cost in China?
The China inspection service rates range from $149 to $320 per man-day which simply means you’ll be looking to pay this rate per product quality inspector per day. On average, this pays for 8-12 hours of product quality inspections time.
Note that inspectors are charged per person per day, so the inspection fees will depend on how long it takes to perform inspection for your goods.
It’s worth noting that all product quality inspections will be priced differently depending on what you need. Some reputable third-party inspection companies will charge additional fees depending on how far their inspector has to travel, which may involve you needing to pay for additional man-days.
This goes without saying, but as part of your inspection, sampling, photographs, and your product inspection report should be included in the price. If the third-party inspection company you’ve chosen tries to charge you more for a report, larger sampling sizes, or product photographs, then this is a red flag.
Note:Third Party Inspection Company charges for per man per day.
Understanding the Cost of Quality Inspections in China Service
MAN-DAYS DEFINITION
This general man-day definition: "a unit of one day's work by one person" seems to be the most suitable for all cases. In the quality control industry the man-day is considered as a workload unit, which is very similar. From the buyer's point of view, the "man-day" is a system that allows direct and quick QC cost calculations.
"Man": both women and men work as inspectors. Qualified staff is crucial for reliable quality control. Inspectors spend their time checking products quality and conformity in factories in order to protect the importers' interests.
"Days": a meaningful inspection takes four to six hours. Inspectors should only perform one QC per day, to ensure reliable results.
Most third-party QC providers, including TESTCOO, will bill you for their inspection services using what are called “man-days”. Man-days are a unit of time for measuring how long one inspector is needed for a service. The number of hours in a man-day can vary by QC provider.
- QC inspection budget
- Traveling to the factory or inspection site (often for an hour or more)
- Preparing the inspection area, which can vary depending on the readiness of the facility
- Pulling a random sample of goods (when using acceptance sampling)
- Writing the inspection report on-site
- Submitting the report to technical staff in the home office for review and approval
- Returning from the factory or inspection site
All of these activities take time and all contribute to the time allotted in a standard man-day. It’s a 12-hour job that involves a lot more than one typically thinks. And depending on the time needed for these, your inspector may have less time to actually examine and test your product than you might expect.
In addition to labor costs, travel expenses may also apply if the factory is far from the nearest importer.
How the Number of Units Inspected Affects Your Inspection Costs
For most consumer goods, it’s usually impractical to inspect 100 percent of an order of hundreds or thousands of units. Instead, third-party Inspection Company will often suggest inspecting a random sample from which the overall quality level of the shipment can be inferred.
What If Your Budget is Low?
What can you do if the budget is too high (maybe your entire order is worth $500)?
Here Are Some Alternatives:
- Find some companies that charge low fees ($249, TESTCOO), but you need to keep your eyes open and carefully identify the quality of their services.
- Ask the supplier for many photos and possibly a live video showing many photos (easy for WeChat in China).
- Ask the supplier to send you some production samples.
- Maybe you can’t buy “Chinese products” directly while keeping the risk low. You need to work with wholesalers.
For most importers, cost is a major factor. You probably don’t want to take the chance of shipping your goods to customers without verifying the quality first. At the same time, you don’t want to pay more than necessary to get a reasonable inspection scope.
Managing costs can be challenging for importers working with one of dozens of professional QC providers offering their services. The best QC provider for you may be one that’s conscious of your budget and willing and able to work with you to accommodate it.
What Are the 4 Types of Quality Inspection?
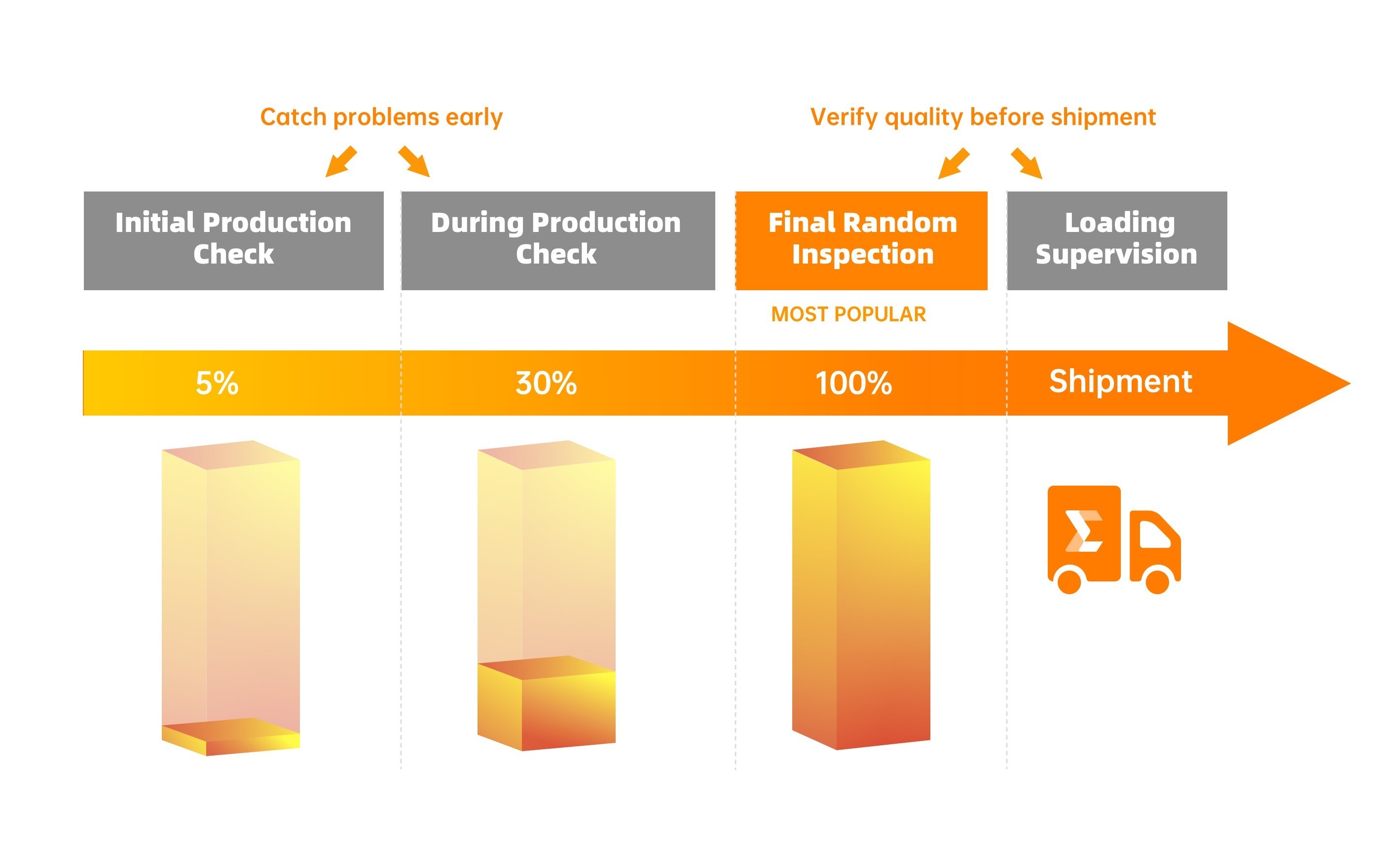
Initial Product Inspection(IPC)
It is performed at the stage of about 5%-10% of products finished for inspection, to allow the revision of product quality requirements before the start of mass production. It allows timely corrections of any non-conformities detected, and improvement actions to be made prior to mass production.
During Production Inspection (DPI)
It is performed at the stage of 30%- 50% goods finished and packed into export cartons. This inspection validates the initial production process has been maintained and that goods being produced continue to meet quality requirements. In the case of new raw materials, new operators, production lines or specification changes, this service can assess if requirements are being met during production.
It is the most effective inspection that confirms the whole shipment's quality level. It normally requires the production to be 100% complete and at least 80% of goods to be packed into cartons. The checked samples are randomly selected according to AQL standard.
It provides witness to the loading process, to make sure the correct quantity and cartons in good condition are loaded into containers in good condition. Container Loading Supervision is an important step in receiving quality goods.
How to Arrange a China Quality Inspection Service?
Suppose you want to arrange for a quality inspection of your product in China.
- Supplier contact information, factory address (otherwise, they will ask for it from the supplier)
- Product description, photos, maybe a short video
- Description of packaging
- State your quality standards and what you can/can’t accept.
- Quantity classification (for example, if there are multiple models, sizes, or colors, they need to know)
Also, if possible, make sure they have physical samples on hand. It’s helpful because some aspects of touch and feel don’t communicate well, even in the video…
Number | Company | Main Service | Company Location | Contact |
1 | TESTCOO | Inspection company in China, | Hangzhou | service@testcoo.com |
product inspection , factory audit , Amazon FBA inspection | ||||
2 | SGS | Testing, inspection, certification | Switzerland/Shanghai | +86 400 099 6058 |
online@sgs.com | ||||
3 | Intertek | Assurance, testing, inspection, certification | UK/Shenzhen | service.china@intertek.com |
4 | TÜV Rheinland | Testing/assessment, certification/auditing, training, inspection/Supervision, consulting/project management | Germany/Beijing | 4001183833 |
5 | TÜV SÜD | Testing and product certification, Auditing and system certification, Inspection, training, advisory | Germany /Shanghai | info@tuvsud.com |
+86 21 6141 0123 | ||||
6 | UI | Certification, testing | Beijing | customerservice.cn@ul.com |
7 | CCIC | China certification and inspection Company; | Beijing | ccic@ccic.com |
inspection, identification, certification and testing | ccic-insp@ccic.com | |||
8 | CTI | Testing company in China, | Shenzhen | info@cti-cert.com |
Testing, certification, inspection, training, audit | ||||
9 | QIMA | Testing, inspection, audit, certification, professional services, software solutions | Hong Kong | 400 009 8282 |
10 | V-Trust | Inspection company in China, | Guangzhou | cs@v-trust.com |
Quality control, supplier evaluation, laboratory | -89089814 | |||
11 | GRGTEST | Testing company in China, | Guangdong | grgtest@grgtest.com |
Measurement and Calibration, Environmental and Reliability Testing, Safety Test and Certification | ||||
12 | TradeAider | Inspection company in China, | Hangzhou | service@tradeaider.com |
product inspection, factory audit | -88397267 | |||
13 | TTS | 3rd quality control company in China | Guangzhou | service@ttsglobal.net |
Inspection, Suppliers Audit, Testing Services | ||||
14 | CIS China Inspection Service | Inspection company in China, | Hong Kong | info@china-inspection-service.com |
Factory Audit and Product Inspection services | ||||
15 | AQF | Inspection company in China, | Shenzhen | asia@asiaqualityfocus.com |
Product Inspection, Supplier Audit, Lab Expertise | sales@asiaqualityfocus.com | |||
16 | Sofest | Supply chain management, product engineering, quality assurance | HongKong | inquiries@sofeast.com |
+852 8175 8177 | ||||
17 | AQI Service | Product inspection, audit and testing | HongKong | info@aqiservice.com |
18 | Pro QC | Product quality, factory & supplier audits, management system audits | Shenzhen | +86 755-2681 7742 |
19 | Tetra Inspection | Product inspection, supplier audit, Certificate | Shenzhen | sales@tetrainspection.com |
20 | AmSpec | Testing, inspection, certification | Hong Kong | internationaldesk@amspecgroup.com |
21 | CIS Commodity Inspection Services | Inspections, analysis, CU TR Certification, Sudan SSMO | Netherlands | info@cis-inspections.com |
22 | Cotecna | Tailor-made inspection, audit, certification and testing | Switzerland | cotecna.shanghai@cotecna.com.cn |
23 | eurofins | A world leader in food, environment, pharmaceutical and cosmetic product testing, discovery pharmacology, forensics, advanced material sciences. | France | info@eurofins.com |
24 | Vicc | Inspection company in China, | Beijing | info@vicc.com |
Inspection, audit, testing, certification | ||||
25 | Inspectaman | Inspection company in China, | Guangdong | book@inspectaman.com |
Product inspection | ||||
26 | VIS Quality Control | Product inspections, testing, factory audits, certifications | Vietnam | Info@vnvis.com |
+84 28 2218 0050 | ||||
27 | Global Inspection Managing | Manufacturing audits, onsite inspections | Hong Kong | (+852) 8176 7196 |
28 | INSIGHT Quality Service | Product inspection, factory audits | US/Shenzhen | info@insight-quality.com |
29 | QGS | Product quality inspection services, factory audit | Hong Kong | ivan@qgs.com.cn |
+86 18929520552 | ||||
30 | Global Trade Specialists | Product design, engineering, prototyping, and production sourcing | Italy | 888-203-2833 |
31 | Supplyia Full inspection | China full inspection service | Yiwu | +86 17280580283 |
How To Work with an Inspection Company in China?
Following these advices can be very helpful for your business.
1. Choose a China Inspection Agent that Understands Your Specifications and Standards
2. Make Sure the People Working in the Factory Know What You Can’t Accept
What types of defects are acceptable, what problems must be kept to a tiny number, and what is an absolute disaster. (This is part of a good spec.)
3. Develop a Proper Inspection Plan
It may include inspection of major components, the first finished product, or final sampling. The goal is to cover the main risks identified.
4. Communicate in the Right Way
Don’t say, “We will send a third party QC company,” as this may scare some suppliers. Instead, it should say, “We are working with China inspection agents to confirm the quality of the goods prior to dispatch.”
5. Agree on Who Should Pay and How Much.
There are two corners here. If your order is over $10,000, you may be able to get your supplier to agree in writing that they will reimburse you for re-inspections in case serious quality issues are discovered.
I suggest simple wording like this:
[Buyer] reserves the right to perform the following quality control activities and any other activities not described below.
China Quality Control Inspection Services:Random inspection of products according to ISO2859-1 standard (single-stage,normal severity,level depends on the situation).The Acceptance Quality Limit(AQL) is 0% critical defects,2.5% major defects,and 4.0% minor defects.
If products inspection is rejected,[Buyer] has the right to request a re-inspection,the cost of which will be re-invoiced to [Supplier].And so on until [Buyer] accepts inspection.
If found defective or out of specification,[Supplier] will inspect the entire quantity and sort it from the bulk quantity,if re-production is not possible,[Supplier] shall notify [Buyer] immediately.
On the other hand, if your order is very low, the opposite may result in you may have to pay the supplier $20-$50 for extra (someone to help unpack and repack the shipment, coordinate dates with the QA agent, etc.).
6. Provide Feedback on the QC Report
If inspectors are too lax or too strict, make sure their standards are adjusted appropriately in the future. We often see QA as a facilitator of communication if done well. Feedback is immediately passed on to all employees in the plant.
7. Remain Firm on Quality Standards
If suppliers push back, reiterate that quality inspections are non-negotiable. Frame them as company policy or a client requirement.
Conclusion
Collaborating with a reliable inspection company in China can save time, reduce risks, and ensure consistent product quality. Whether you're dealing with large or small orders, developing a basic quality control plan tailored to your needs is essential.
For professional inspection services, factory audits, or Amazon FBA inspections, contact TESTCOO. Let us help you achieve quality excellence. Submit an inquiry today to receive a customized quote!
Free Sample Report Performance Quality Control
Download a sample report to keep control of your supply chain!
Featured Articles
- AQL Table | How to Read It
- TOP 10 Common Defects in Garments Quality Inspection
- Product Packaging and Shipment Label requirements for Amazon FBA
- What Is ASTM-F2413-18? Protective Footwear Standard
- How to Conduct Third-Party Quality Control Inspections for Electric Scooters
- SMETA Audit-What is SMETA Audit?
- TESTCOO Supplier Verification/Certification Service SLCP, Higg FEM, GRS, GOTS
- Quality Control Inspection Company in China
- What is Quality Inspection? A Complete Guide
- Guidelines for Product Inspection in India
Category
- Production Inspection Service
- Factory Audit
- Softline Inspection
- Hardline Inspection
- Electrics Inspection
- Certification
- Checklist
- Manufacturers
- Quality Assurance Basics
- Products Recall
- AQL
- Guidence and Standard
- News
- Supplier Management
- Amazon
- Protective Equipment
- e-commerce quality control
- Indian Manufacturing
- Soft Goods Quality Control
- Supply Chain Management
- Supply Chain Resilience
- E-Commerce Quality Control
- ISO 2859
- Supply Chain Optimization
- Garment Industry
- Higg Index