Navigating U.S. Tariffs on China in 2025: How Third-Party Inspections Can Help Mitigate Supply Chain Risks
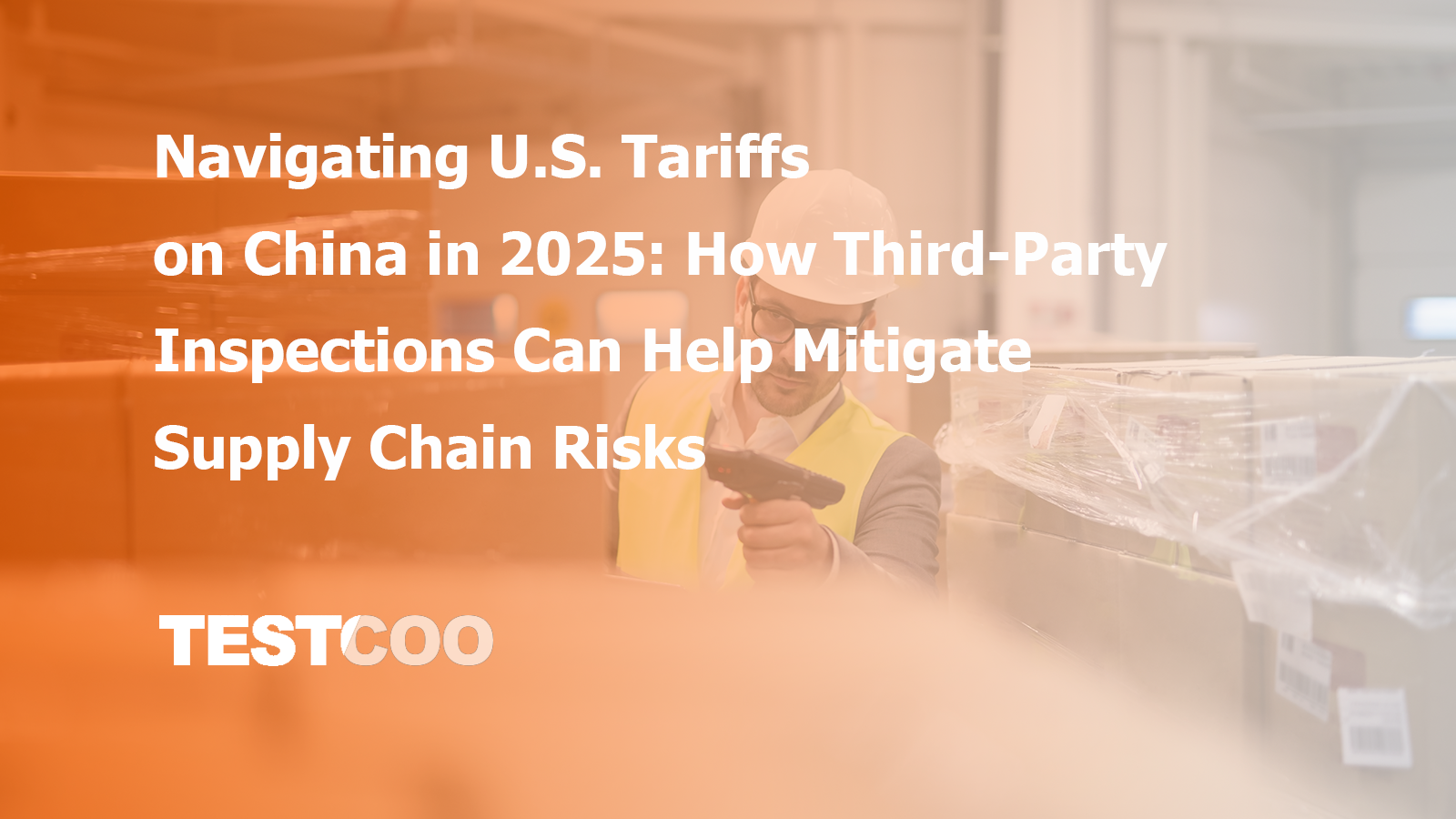
The global trade landscape is once again facing uncertainties as the U.S. government, under former President Donald Trump’s new policies, implements additional tariffs on Chinese goods in 2025. These tariffs will have far-reaching implications for businesses that rely on Chinese manufacturing. From increased production costs to disrupted supply chains, companies must find ways to adapt and minimize risks.
One crucial strategy that can help mitigate these risks is leveraging third-party inspection services. Ensuring product quality, compliance and transparency has never been more essential. This blog explores the impact of the new tariffs, the challenges businesses face and how third-party inspections can play a key role in navigating these changes.
Understanding the 2025 U.S. Tariffs on China
What Are the New Tariffs?
The U.S. administration has reinstated and expanded tariffs on Chinese imports, targeting industries such as electronics, textiles, machinery and consumer goods. While the exact tariff percentages vary, they aim to encourage domestic manufacturing and reduce reliance on Chinese supply chains.
For the latest tariff updates, visit the U.S. Trade Representative (USTR) website.
Why Are These Tariffs Being Imposed?
The rationale behind these tariffs includes:
- Protecting U.S. industries from foreign competition
- Addressing trade imbalances
- Reducing reliance on Chinese supply chains
- National security concerns related to technology and critical infrastructure
These tariffs increase import costs, leading to price hikes, supply chain shifts and operational changes for businesses sourcing from China.
Read more: Fact Sheet: President Donald J. Trump Imposes Tariffs on Imports from Canada, Mexico and China
Different industries will experience varying levels of disruption. For example:
- Apparel and Textiles: Increased production costs may force brands to seek alternative manufacturing hubs.
- Electronics: The semiconductor and hardware industry may face higher operational expenses.
- Automotive: Tariffs on Chinese-made components can lead to increased vehicle prices.
- Consumer Goods: A broad category that will experience direct price hikes on everyday products.
By understanding these impacts, businesses can develop proactive strategies to mitigate risks and sustain profitability.
↵
↵
Challenges Businesses Face Due to Tariffs
1. Rising Costs of Goods and Production
Higher tariffs mean higher import costs. Businesses must either absorb these costs, pass them on to consumers, or look for alternative sourcing options. These additional expenses impact competitiveness and profit margins.
2. Increased Supply Chain Complexity
Many companies are considering moving production to alternative countries like Vietnam, India, or Mexico. However, shifting supply chains comes with logistical, quality and compliance risks. Establishing new vendor relationships takes time and not all suppliers meet international standards.
For navigating uncertainty in Asia’s supply chains, check this industry report.
3. Compliance and Quality Concerns
Tariffs increase the need for businesses to ensure that their imported goods meet U.S. regulations. Without rigorous inspection and quality control, companies risk non-compliance, leading to costly fines, product recalls and reputational damage.
To ensure compliance, review U.S. Customs and Border Protection (CBP) guidelines.
4. Counterfeit and Substandard Products
To offset rising costs, some suppliers may cut corners, using inferior materials or engaging in fraudulent practices. Without proper verification, businesses risk receiving non-compliant or defective products, which can lead to consumer dissatisfaction and legal implications.
5. Disruptions in Delivery and Lead Times
Higher costs and supply chain shifts may cause delays in production and shipping, making it difficult to meet market demand. Businesses need to plan ahead and incorporate buffer times to mitigate these disruptions.
How Third-Party Inspections Help Mitigate Supply Chain Risks
1. Ensuring Product Quality and Compliance
Third-party inspection companies conduct initial production check, during production check and final random inspections to ensure products meet international quality standards, safety regulations and U.S. import requirements. This prevents costly rejections and recalls, ensuring products are safe, functional and compliant.
For details on AQL standards, visit ISO 2859-1.
2. Verifying Supplier Credibility
Before sourcing from a new supplier, businesses can rely on factory audits and supplier verification to ensure credibility, ethical practices and production capability. A thorough background check can prevent financial and operational risks.
Find more information: 7 Types of Factory Audits that Help to Evaluate Your Supplier
3. Reducing Defect Rates and Returns
With tariffs increasing overall costs, minimizing defects is critical. Quality control inspections help identify issues early, preventing defective shipments and reducing the risk of customer complaints, refunds, or recalls.
4. Ensuring Correct Labeling and Documentation
U.S. customs and import authorities require proper documentation for compliance. Third-party inspection firms check for correct labeling, certifications and compliance with U.S. tariff regulations, avoiding potential penalties and ensuring smooth customs clearance.
Read our comprehensive guide on Apparel Standards and Regulations in the US
5. Helping with Diversification and Alternative Sourcing
For businesses exploring alternative manufacturing locations due to tariffs, third-party inspection services can assess new suppliers in different countries, ensuring they meet quality and compliance standards before shifting production. This helps businesses diversify supply chains while maintaining product integrity.
6. Preventing Ethical and Social Compliance Issues
Many countries have strict regulations on ethical sourcing, labor practices and sustainability. Third-party inspections ensure that suppliers meet these standards, preventing legal repercussions and brand reputation damage.
Read more: Understanding C-TPAT: The Key to Secure Trade with the U.S.
For insights into third-party inspection benefits, visit Testcoo’s inspection services.
Conclusion
The 2025 U.S. tariffs on Chinese goods present challenges, but businesses can navigate these uncertainties by prioritizing quality control and supply chain transparency. Third-party inspection services play a critical role in reducing risks, ensuring compliance and maintaining product standards. As global trade policies continue to evolve, partnering with trusted inspection companies like Testcoo can help businesses stay ahead and adapt to changing market conditions.
Need expert guidance on quality inspections? Contact Testcoo today to safeguard your supply chain against tariff-related risks!
Free Sample Report Performance Quality Control
Download a sample report to keep control of your supply chain!
Featured Articles
- AQL Table | How to Read It
- TOP 10 Common Defects in Garments Quality Inspection
- Product Packaging and Shipment Label requirements for Amazon FBA
- What Is ASTM-F2413-18? Protective Footwear Standard
- How to Conduct Third-Party Quality Control Inspections for Electric Scooters
- SMETA Audit-What is SMETA Audit?
- TESTCOO Supplier Verification/Certification Service SLCP, Higg FEM, GRS, GOTS
- Quality Control Inspection Company in China
- What is Quality Inspection? A Complete Guide
- Guidelines for Product Inspection in India
Category
- Production Inspection Service
- Factory Audit
- Softline Inspection
- Hardline Inspection
- Electrics Inspection
- Certification
- Checklist
- Manufacturers
- Quality Assurance Basics
- Products Recall
- AQL
- Guidence and Standard
- News
- Supplier Management
- Amazon
- Protective Equipment
- e-commerce quality control
- Indian Manufacturing
- Soft Goods Quality Control
- Supply Chain Management
- Supply Chain Resilience
- E-Commerce Quality Control
- ISO 2859
- Supply Chain Optimization
- Garment Industry
- Higg Index