Detailed Explanation of Third-Party Inspections: FAI, IPC, DUPRO, FRI, PSI, CLC
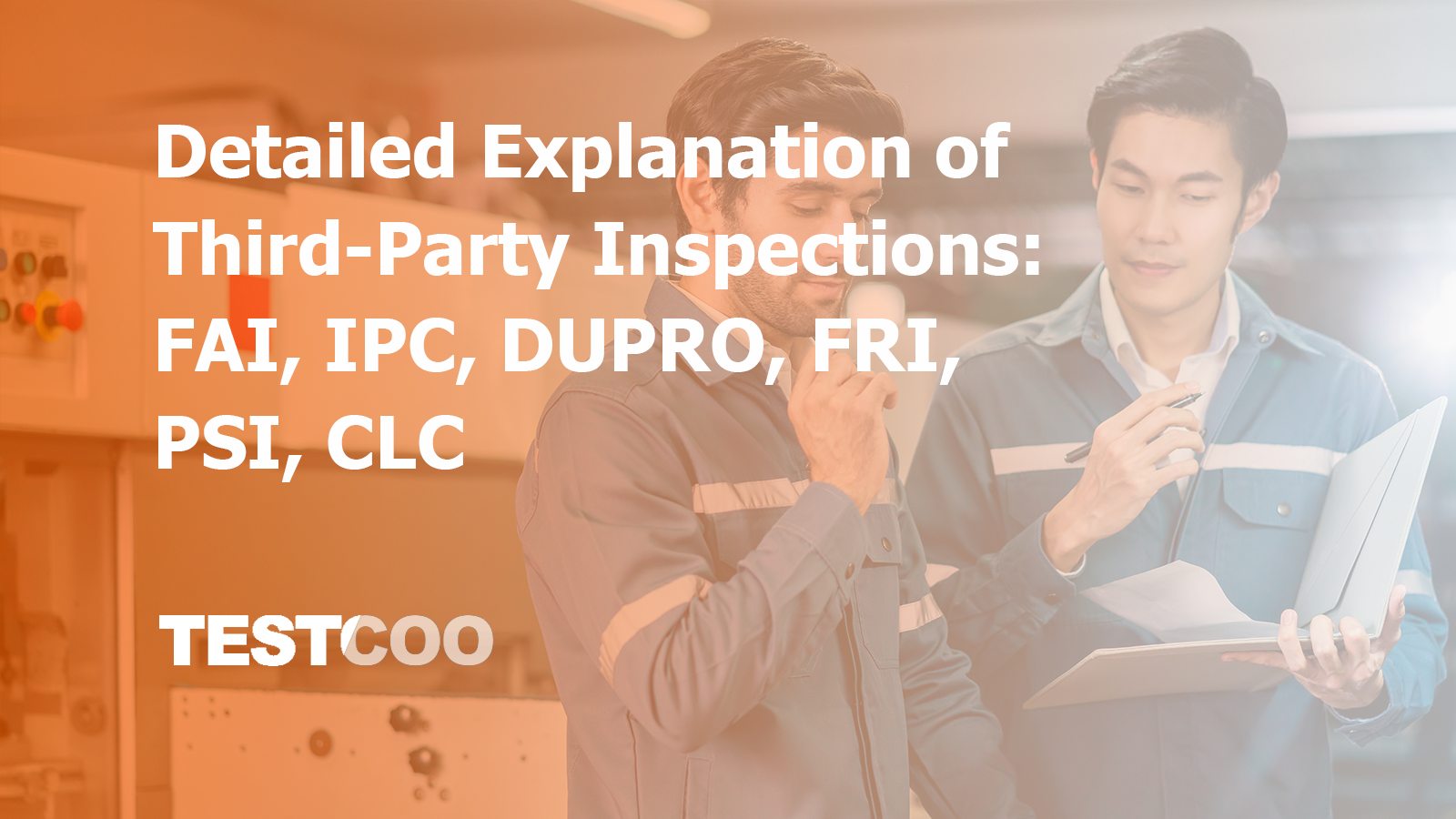
↵ ↵ ↵ ↵ ↵ ↵ ↵ ↵
In international trade and manufacturing, Third-Party Inspection plays a critical role. Especially in the globalized supply chain, the geographical distance between manufacturers, suppliers and customers makes quality control increasingly complex. Third-party inspections provide an effective solution by employing external professional agencies to ensure that product quality meets the required standards.
During third-party inspection processes, several key inspection steps are widely implemented, including First Article Inspection (FAI), Initial Production Check (IPC), During Production Check (DUPRO/DPI), Final Random Inspection (FRI), Pre-Shipment Inspection (PSI), Container Loading Check (CLC), Container Loading Inspection (CLI) and Container Loading Supervision (CLS). This blog provides a detailed explanation of the standards, inspection content, processes and importance of these inspection types.
First Article Inspection (FAI)
First Article Inspection (FAI) is a detailed quality check conducted on the first batch of products at the start of the production process. FAI is a critical step in verifying whether the production process aligns with design and specification requirements, ensuring that the initial batch serves as a standard-compliant sample before mass production.
Standards:
- Product Design and Technical Specifications: FAI is typically conducted according to design drawings, technical specifications and engineering requirements. These standards outline all dimensions, functionalities and physical attributes of the product.
- Customer Design Requirements: Clients provide product requirement documents or specifications, which FAI ensures the initial sample conforms to.
- Engineering Change Control: The FAI process also adheres to Engineering Change Request (ECR) standards to ensure that no unauthorized changes occur during design or production.
Inspection Content:
- Ensures that the sample meets all design requirements and technical specifications.
- Conducts comprehensive checks on dimensions, functionality, appearance and materials.
- Verifies whether the first production batch meets predetermined quality standards.
Process:
- Design Review: Examines design documents to ensure all requirements, standards, specifications and certifications are clearly defined and ready for inspection.
- Material and Component Inspection: Checks raw materials and parts used in production to confirm compliance with quality standards.
- Production Process Check: Assess whether the production process complies with Standard Operating Procedures (SOPs) and quality requirements.
- First Product Manufacture: Produces a single product for detailed quality inspection.
- Record Review: Verifies the quality records of the first product, ensuring all inspection data and results are accurate.
- Verification Report: Generates an FAI report confirming the product meets all design requirements. If issues are found, adjustments and retesting are conducted until the product is approved.
Importance:
- Ensures quality control standards are upheld, providing assurance for subsequent mass production.
- Reduces production errors and costs by validating designs and processes to avoid defects.
- Builds customer trust by confirming production capabilities and quality assurance.
- Mitigates risks by identifying and correcting problems early in the production cycle, especially during new product development.
Read more about the Importance of Third-Party Quality Inspection in Ensuring Excellence in Every Step
Initial Production Check (IPC)
Initial Production Check (IPC) is an early-stage inspection conducted shortly after production begins. Typically performed after the first batch of samples is completed, but before full-scale production starts (5–10% of batch completion).
Standards:
- Customer Production Standards: IPC evaluates production line readiness, equipment setup and raw material quality based on the client's requirements.
- Industry Standards: For example, IEC standards in electronics or OEKO-TEX standards in textiles.
Inspection Content:
- Verifies if production processes adhere to predefined standards and procedures.
- Assess the readiness of equipment and personnel to ensure smooth mass production.
- Checks initial products for compliance with design specifications, including dimensions, appearance and performance.
Process:
- Production Line Readiness: Confirms that all equipment and workers are prepared and operating as expected.
- Process Verification: Ensures production follows established procedures, particularly SOPs.
- Sample Inspection: Extracts samples during initial production for quality checks and evaluates production quality controls.
- Raw Material Checks: Verifies that materials meet standards to maintain overall product quality.
- Progress Tracking: Monitors production progress, identifying and addressing issues promptly.
Importance:
- Detects potential quality issues early to prevent large-scale defects in mass production.
- Improves production efficiency by ensuring seamless operations on the production line.
- Maintains quality control at every stage, ensuring high standards from raw materials to the final product.
- Reduces rework and returns, saving costs by addressing problems early.
Read more: What is Quality Inspection? A Complete Guide
During Production Inspection (DUPRO/DPI)
During Production Inspection (DUPRO/DPI) is an inspection conducted during the production process, typically when 30–50% of the production is completed.
Standards:
- Customer Requirements: Strict adherence to client-defined quality standards for each production stage.
- International Safety and Environmental Standards: For example, IEC standards for electrical safety or environmental compliance.
Inspection Content:
- Checks if products under production meet quality standards.
- Ensures production process stability, preventing defects from improper operations.
- Verifies that the actual production aligns with planned processes, including raw materials, equipment and personnel.
Process:
- Production Progress Tracking: Ensures production stays on schedule.
- Quality Sampling: Randomly selects in-progress or finished products for quality checks.
- Process Validation: Confirms adherence to SOPs and identifies quality control gaps.
- Packaging Readiness: Ensures packaging meets transportation requirements and is prepared for shipment.
Importance:
- Prevents widespread issues by identified defects during production.
- Enhances flexibility by enabling real-time adjustments to production processes.
- Reduces post-production costs by detecting issues early.
- Ensures product consistency in quality and appearance to meet customer expectations.
Read more to learn how a DUPRO can drastically improve your production schedule in the garments sector
Final Random Inspection (FRI)
Final Random Inspection (FRI) is a final-stage inspection conducted after 100% of the goods are produced and at least 80% are packed. This inspection uses random sampling to evaluate the overall quality of the production batch.
Standards:
- AQL Standards: FRI is conducted based on Acceptable Quality Level (AQL) standards, which determine the sample size and allowable defect ratios.
- Product Technical Specifications and Standards: FRI typically follows product technical specifications, contractual requirements and industry standards.
Inspection Content:
- Perform random sampling inspection on a large batch of products.
- Check whether the products meet the quality standards specified in the contract.
- Verify whether qualified products meet the standards for factory release.
Process:
- Random Sampling: Randomly select a certain number of samples from the completed goods for inspection.
- Quality Validation: Check the appearance, functionality and quality of the sampled products against the standards.
- Report Generation: Generate a final inspection report based on the results to confirm product compliance.
- Shipping Decision: Decide whether to ship the goods based on the inspection results. If issues are found, rework or reproduction may be required.
Importance:
- Enhances Overall Quality: By conducting random sampling inspections, FRI evaluates the overall quality level of the batch, ensuring that shipped products meet the standards.
- Reduces Inspection Costs: Compared to inspecting each product individually, FRI saves costs through sampling.
- Improves Supply Chain Efficiency: FRI helps ensure the quality of the entire batch, reduces the occurrence of defective products and enhances overall supply chain efficiency.
Read more: The Importance of Final Random Inspections in Global Trade - Your Guide to Quality Assurance
Pre-Shipment Inspection (PSI)
Pre-Shipment Inspection (PSI) is a comprehensive inspection conducted after production is complete and before goods are shipped. PSI ensures that all items in an order meet the agreed-upon quality standards and quantity requirements.
Standards:
- Contract Requirements and Product Specifications: PSI is conducted according to purchase contracts and client-provided product specifications to ensure all goods meet the agreed standards before shipment.
- International Standards (ISO, IEC, etc.): Depending on the industry, PSI references relevant international standards, such as ISO 9001 , IEC 61000 (electromagnetic compatibility), or FDA standards (for food and medical products).
- AQL Standards : PSI often employs AQL standards to determine the acceptable defect ratios.
Inspection Content:
- Verify the appearance, dimensions, functionality and performance of products to ensure compliance with client requirements.
- Confirm that product quantity, packaging and labeling meet contractual requirements.
- Conduct sampling checks based on AQL standards to determine the maximum tolerance for defective items.
Process:
- Confirm Goods: Verify that the quantity, type and specifications of the products match the contract.
- Product Inspection: Inspect each product to ensure it meets predetermined quality standards.
- Inspection Report Generation: Create an inspection report based on the results to confirm product compliance.
- Packaging Check: Ensure that the product packaging complies with international transportation standards to prevent damage during transit.
- Transportation Arrangement: Confirm the transportation method and readiness of shipping documents.
Importance:
- Ensures Contract Fulfillment: PSI helps buyers confirm that the products comply with contractual requirements, ensuring transparency and reliability in transactions.
- Reduces Risks: PSI ensures product quality meets standards, reducing the likelihood of returns and disputes due to quality issues.
- Guarantees Accurate Shipping: Ensures that product quantity, specifications and appearance align with expectations, avoiding shipping errors.
- Enhances Customer Satisfaction: PSI allows buyers to verify product quality, improving satisfaction and avoid unnecessary disputes.
Container Loading Check (CLC) / Container Loading Inspection (CLI) / Container Loading Supervision (CLS)
Container Loading Check (CLC), Container Loading Inspection (CLI) and Container Loading Supervision (CLS), collectively referred to as container loading monitoring, are inspections conducted before shipment to verify the loading process of goods into containers. These inspections ensure that products are properly loaded and can be safely transported.
Standards:
- Loading Safety Standards: CLC/CLI/CLS adheres to international freight standards, cargo loading safety guidelines and customs regulations to ensure safe loading.
- Client and Contract Standards: Clients usually specify loading requirements in contracts, which are strictly followed during CLC inspections.
Inspection Content:
- Verify the safety of goods during loading to ensure no improper or overloaded conditions exist.
- Ensure all products are loaded correctly and evenly to prevent damage during transit due to imbalances.
- Confirm that the loaded goods match the packing list and contract specifications.
- Check that products are properly packed to prevent damage.
- Supervise the entire loading process to avoid human errors or negligence.
Process:
- Review Loading Plan: Confirm the container loading plan to ensure a reasonable arrangement.
- Supervise Loading: Monitor the loading process to ensure it adheres to safety standards and optimizes space utilization.
- Product Protection Check: Verify that each item is adequately protected during loading to avoid damage during transit.
- Final Confirmation: Check that the quantity and specifications of the loaded goods match the contract and ensure no discrepancies.
Importance:
- Ensures Safe Transportation: CLC ensures goods are securely loaded, minimizing the risk of damage during transit.
- Improves Transportation Efficiency: Proper loading methods enhance container utilization and reduce shipping costs.
- Prevents Loading Errors: Supervising the loading process reduces errors and ensures accurate deliveries.
Implementing Effective Product Quality Inspections for Your Business Success with Testcoo
Each step of third-party inspection has its unique role and process. Through these measures, businesses can effectively ensure product quality, reduce production risks and build customer trust. In a globalized supply chain, third-party inspections such as Testcoo are not just tools for quality control but are also vital for maintaining brand reputation and enhancing customer satisfaction.
Get in touch with our team of inspection specialist to get a sample report.
Want Us To Ensure Your Product Quality?
Request a demo to see our report details to know more. Worth to contact us to get reliable, efficient and comprehensive quality control services. We will arrange an inspection for you, anytime, any where.
Free Sample Report Performance Quality Control
Download a sample report to keep control of your supply chain!
Featured Articles
- AQL Table | How to Read It
- TOP 10 Common Defects in Garments Quality Inspection
- Product Packaging and Shipment Label requirements for Amazon FBA
- What Is ASTM-F2413-18? Protective Footwear Standard
- How to Conduct Third-Party Quality Control Inspections for Electric Scooters
- SMETA Audit-What is SMETA Audit?
- TESTCOO Supplier Verification/Certification Service SLCP, Higg FEM, GRS, GOTS
- Quality Control Inspection Company in China
- What is Quality Inspection? A Complete Guide
- Guidelines for Product Inspection in India
Category
- Production Inspection Service
- Factory Audit
- Softline Inspection
- Hardline Inspection
- Electrics Inspection
- Certification
- Checklist
- Manufacturers
- Quality Assurance Basics
- Products Recall
- AQL
- Guidence and Standard
- News
- Supplier Management
- Amazon
- Protective Equipment
- e-commerce quality control
- Indian Manufacturing
- Soft Goods Quality Control
- Supply Chain Management
- Supply Chain Resilience
- E-Commerce Quality Control
- ISO 2859
- Supply Chain Optimization
- Garment Industry
- Higg Index