Consumer Electronics Inspection: A Complete Guide for Global Buyers
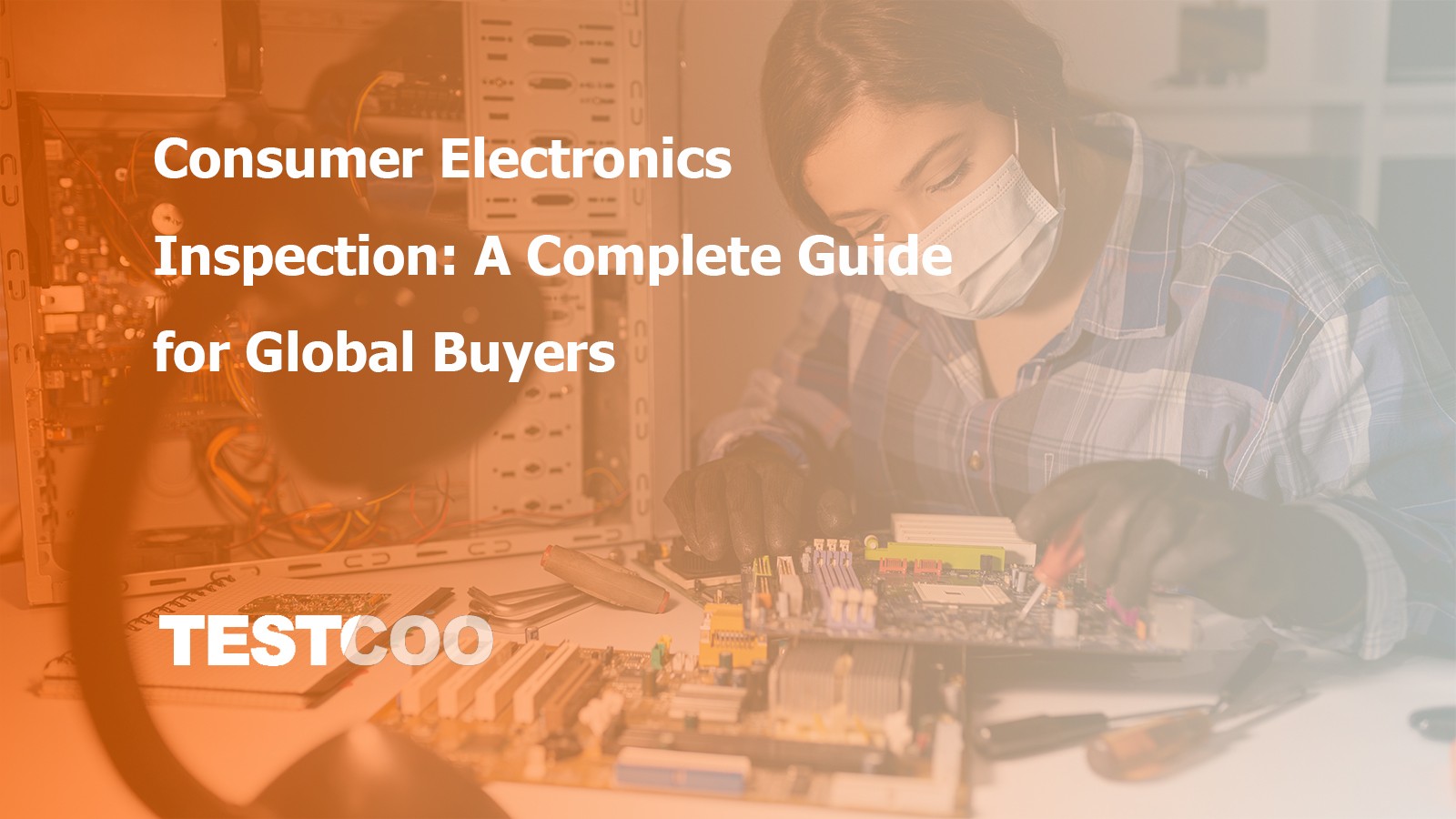
↵ ↵ ↵ ↵ ↵ ↵ ↵ ↵ ↵ ↵ ↵
↵ ↵
↵ ↵
In today’s fast-paced, tech-driven world, consumer electronics have become essential to everyday life. From smartphones and laptops to smartwatches and home appliances, the demand for reliable, safe and high-performing electronic products is higher than ever. For global buyers and brands, ensuring product quality and compliance isn’t just a preference, it’s a necessity. This is where consumer electronics inspection plays a vital role.
In this comprehensive guide, we’ll dive into what consumer electronics inspection involves, why it’s critical, the types of inspections available, common defects found and how working with a reliable third-party inspection company can help you deliver products that meet international standards and customer expectations.
Table of Contents
What is Consumer Electronics Inspection?Why is Consumer Electronics Inspection Important?Types of Consumer Electronics InspectionsKey Checkpoints During InspectionCommon Defects in Consumer ElectronicsGlobal Standards & Compliance RequirementsBenefits of Third-Party Inspection ServicesHow to Choose the Right Inspection PartnerCase Example: Electronics Inspection in ChinaConclusion↵
↵
1. What is Consumer Electronics Inspection?
Consumer electronics inspection is a comprehensive quality control process designed to ensure the performance, safety and appearance of electronic products used in everyday life. These products range from smartphones and tablets to kitchen appliances, wearables and personal care electronics. Given the complexity of their internal components and the importance of user safety, maintaining strict quality standards is essential.
The core purpose of consumer electronics inspection is to verify that each item is:
- Functionally sound (e.g., switches, buttons, displays and connectivity work properly),
- Safe to use (free from electrical, thermal or mechanical hazards),
- Visually acceptable (with no scratches, dents or misaligned parts), and
- Compliant with relevant international safety and performance standards (such as CE, FCC, RoHS or UL).
To achieve this, inspections are strategically conducted at multiple stages across the supply chain. This includes an Initial Production Check (IPC) to validate materials and components, a During Production Inspection (DUPRO) to catch issues early during mass manufacturing and a Final Random Inspection (FRI) or even 100% Inspection before shipment to ensure the final batch meets quality expectations. These inspections are vital tools for reducing defects, avoiding costly recalls and protecting both consumers and brand reputation in the global market.
2. Why is Consumer Electronics Inspection Important?
Here are key reasons why inspections are essential:
Quality Assurance - Consumer electronics are complex products with sensitive components. A minor issue with a circuit board, soldering or battery can lead to malfunctions or product failure.
Safety and Compliance - Faulty electronics can pose fire, explosion or electrical shock hazards. Inspections help ensure compliance with safety standards such as CE, FCC, RoHS and others.
Brand Reputation - One defective product can damage a brand’s reputation, especially in a highly competitive industry.
Cost Efficiency - Detecting issues early prevents costly returns, recalls and warranty claims.
Customer Satisfaction - Reliable, defect-free products lead to better reviews, fewer complaints and stronger brand loyalty.
3. Types of Consumer Electronics Inspections
Initial Production Check (IPC)
- Checks raw materials and components before production starts.
- Verifies supplier capability and process readiness.
During Production Inspection (DUPRO)
- Conducted when 20-80% of production is complete.
- Helps monitor quality during production and catch issues early.
- Conducted when at least 80% of goods are packed.
- Includes full checks on function, appearance, safety, labeling and packaging.
Laboratory Testing
- Performed to check compliance with specific safety and performance standards.
- Can include chemical analysis, drop tests, waterproof testing and more.
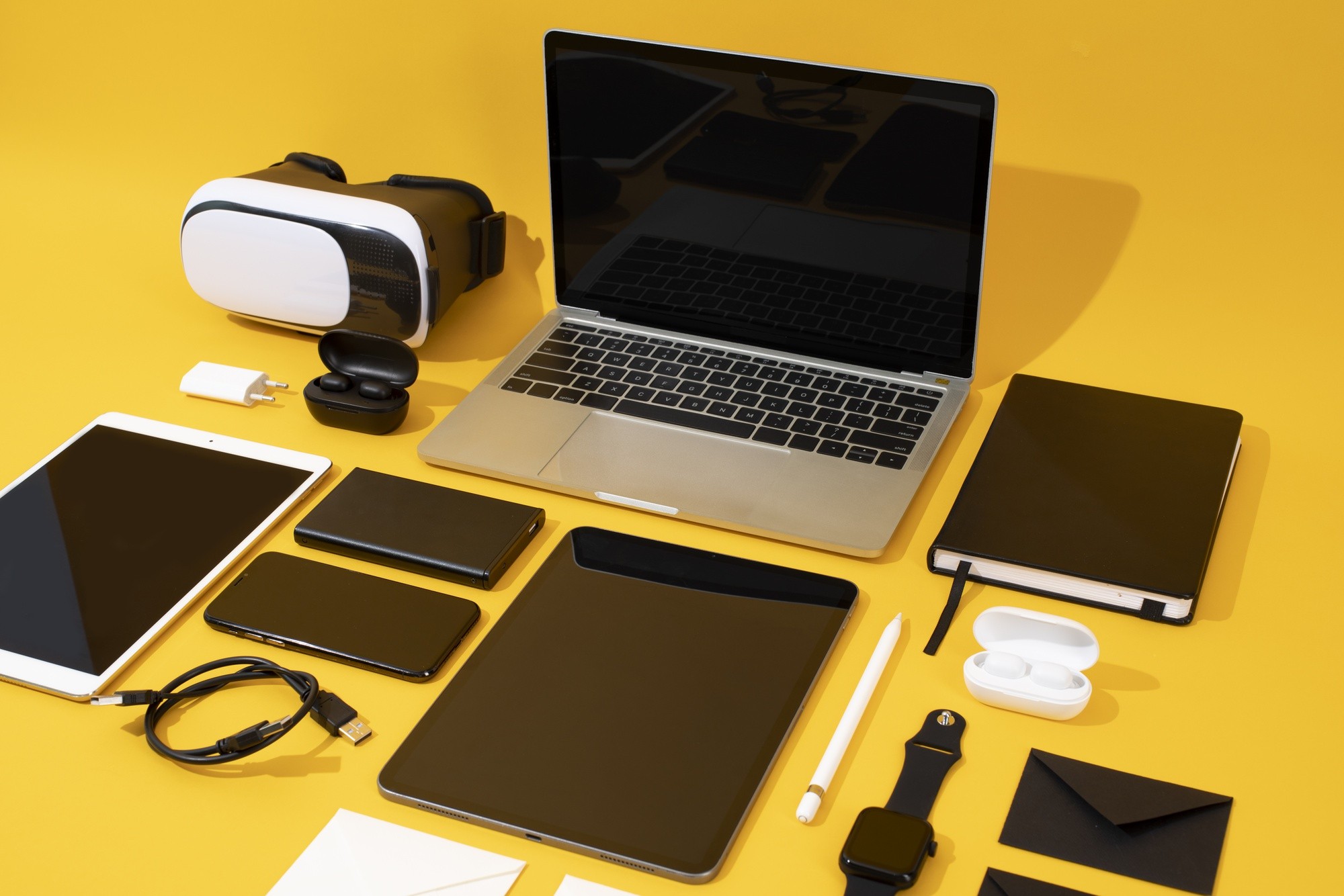
4. Key Checkpoints During Inspection
During a consumer electronics inspection, trained inspectors follow a detailed checklist to evaluate every aspect of the product to ensure it meets quality, safety and performance standards.
Functionality Tests - Inspectors begin by checking whether the product powers on and off correctly. They verify that all essential functions, such as buttons, touchscreens and display panels, are responsive and operational. Any smart features or modes are also tested to ensure full functionality.
Battery and Charging - Battery performance is a critical aspect. Inspectors test battery life under normal use conditions, check for signs of overheating during charging and verify the performance and safety of charging cables, ports and adapters.
Packaging and Labeling - Proper packaging protects the product in transit. Inspectors ensure that packaging is secure, tamper-proof and correctly labeled with barcodes, product names, safety warnings and instructions.
Workmanship and Appearance - The product is carefully examined for surface scratches, dents, poor finishes, gaps or misaligned parts. Soldering quality and casing uniformity are also reviewed.
Connectivity Features - For smart devices, inspectors test WiFi, Bluetooth, GPS and any other connectivity functions for speed and reliability.
Documentation - Manuals, warranty cards and certification labels must be complete, legible and correctly included.
Performance Testing - Additional performance metrics like boot-up time, speaker output, display resolution and touchscreen responsiveness are also tested to ensure the device performs as expected.
Explore our guide on Amazon Electronics Requirements for Sellers
5. Common Defects in Consumer Electronics
Consumer electronics are intricate products and even minor flaws can lead to major issues. Quality defects generally fall into four key categories:
Functional Defects - These are issues that directly impact how the product operates. Common examples include devices that fail to power on, unresponsive touchscreens or buttons and inconsistent charging or battery drainage problems. These types of defects severely affect the user experience and often lead to product returns or customer dissatisfaction.
Safety Defects - Electronics that overheat, short circuit or have poorly insulated wiring pose serious safety hazards. Such defects can result in fire, electric shock or other dangers, especially in battery-powered or plug-in devices. These issues must be addressed immediately to ensure compliance with global safety standards.
Visual Defects - Aesthetic imperfections such as scratches, dents or cracks on the casing or misaligned screens, buttons or logos, reduce the perceived value of the product. These are especially critical in premium consumer segments where look and feel matter greatly.
Packaging Defects - This includes missing accessories, misprinted or damaged user manuals or inadequate packaging that fails to protect the product during shipping. These defects not only frustrate customers but can also damage your brand reputation.
Such issues often stem from inadequate quality control or a lack of skilled labor, making professional third-party inspections essential for identifying and addressing them early in the supply chain.
6. Global Standards & Compliance Requirements
Depending on the destination market, products must comply with:
Failing to meet these standards can result in fines, import bans or brand damage.
Discover the Countries which Accept CE Marked Products
7. Benefits of Third-Party Inspection Services
Partnering with a third-party inspection company brings many advantages:
Unbiased Evaluation - Third-party inspectors offer independent, objective insights, unlike in-house teams who may be under internal pressure.
Expertise and Equipment - Professional inspectors are trained in electronics and use calibrated tools to detect even subtle defects.
Global Reach - For companies sourcing from China, Vietnam, India or other countries, a third-party provider like Testcoo can deliver consistent quality control worldwide.
Faster Decision Making - Detailed reports with photos and results help buyers decide whether to approve, reject or rework a batch saving time and cost.
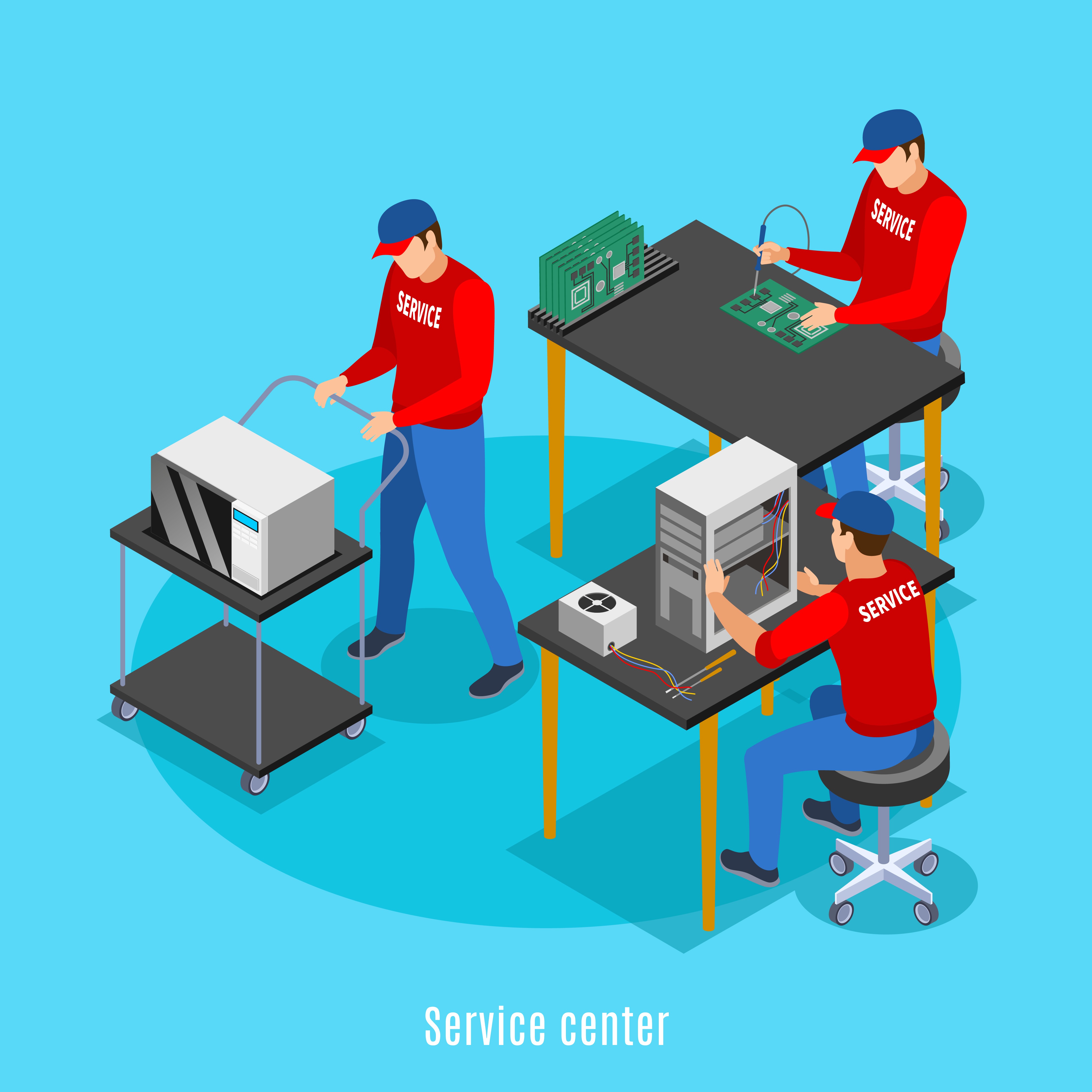
8. How to Choose the Right Inspection Partner
Choosing the right third-party inspection provider is a critical decision that directly impacts your product quality and brand reputation. Here are key factors to evaluate:
Proven Experience in Consumer Electronics - Ensure the inspection company has extensive experience handling a wide range of electronic products. They should have technical know-how in electrical safety, compliance testing, functional performance and quality control standards such as CE, FCC and RoHS. Industry knowledge reduces the chances of oversight.
Global Inspection Network - Look for a provider with inspection capabilities in your primary sourcing countries—especially major manufacturing hubs like China, Vietnam, India and others. A global network ensures consistent service quality and faster deployment of inspectors wherever needed.
Transparent and Detailed Reporting - An effective inspection partner should provide easy-to-understand, visual-rich reports. These reports should include detailed checklists, photographs, defect classifications and clear recommendations to support informed decision-making.
Real-Time Digital Access - Modern inspection services should offer online portals or mobile apps where you can access reports, track inspections and approve results remotely in real time.
Speed and Reliability - Time is money. A good partner will deliver inspection results within a short timeframe, preventing delays in shipping and ensuring you stay on schedule.
Find top 10 Quality Control Inspection Companies in India
9. Case Example: Electronics Inspection in China
China remains a major hub for electronics manufacturing. However, due to the high volume and fast-paced production, quality issues can often arise without strong oversight.
A buyer sourcing Bluetooth speakers from a factory in Shenzhen partnered with a Testcoo, a leading third-party inspection company in China. During an Initial Production Check, inspectors found:
- 20% of units had connectivity issues
- Several units had packaging missing barcodes
- Incorrect voltage ratings printed on adapters
Thanks to early detection, the buyer rejected the shipment, had the factory rework the products and avoided a major product recall.
10. Conclusion
As consumer expectations rise and global competition increases, product quality and safety can make or break your brand. Consumer electronics inspection is no longer optional—it’s a strategic necessity for any serious buyer or brand.
Whether you're sourcing smartwatches, earphones, tablets or home gadgets, partnering with a reliable third-party inspection company ensures:
- High-quality products
- Compliance with global standards
- Reduced risks and returns
- Satisfied customers and stronger brand trust
Need help with your electronics inspections?
At Testcoo, we specialize in delivering professional, efficient and dependable inspection services across Asia’s major manufacturing hubs. Whether you're sourcing consumer electronics, apparel, home goods or industrial components, our experienced team ensures your products meet international quality and safety standards—from pre-production to final shipment. We help brands and buyers minimize risks, avoid costly defects and build stronger supplier relationships through our transparent, real-time reporting and consistent service quality. With our deep industry expertise and presence across key sourcing regions like China, Vietnam and India, we’re here to support your growth.
Get in touch today to schedule an inspection.
Free Sample Report Performance Quality Control
Download a sample report to keep control of your supply chain!
Featured Articles
- AQL Table | How to Read It
- TOP 10 Common Defects in Garments Quality Inspection
- Product Packaging and Shipment Label requirements for Amazon FBA
- What Is ASTM-F2413-18? Protective Footwear Standard
- How to Conduct Third-Party Quality Control Inspections for Electric Scooters
- SMETA Audit-What is SMETA Audit?
- TESTCOO Supplier Verification/Certification Service SLCP, Higg FEM, GRS, GOTS
- Quality Control Inspection Company in China
- What is Quality Inspection? A Complete Guide
- Guidelines for Product Inspection in India
Category
- Production Inspection Service
- Factory Audit
- Softline Inspection
- Hardline Inspection
- Electrics Inspection
- Certification
- Checklist
- Manufacturers
- Quality Assurance Basics
- Products Recall
- AQL
- Guidence and Standard
- News
- Supplier Management
- Amazon
- Protective Equipment
- e-commerce quality control
- Indian Manufacturing
- Soft Goods Quality Control
- Supply Chain Management
- Supply Chain Resilience
- E-Commerce Quality Control
- ISO 2859
- Supply Chain Optimization
- Garment Industry
- Higg Index