Lighting Inspection: Types of Tests and Global Standards
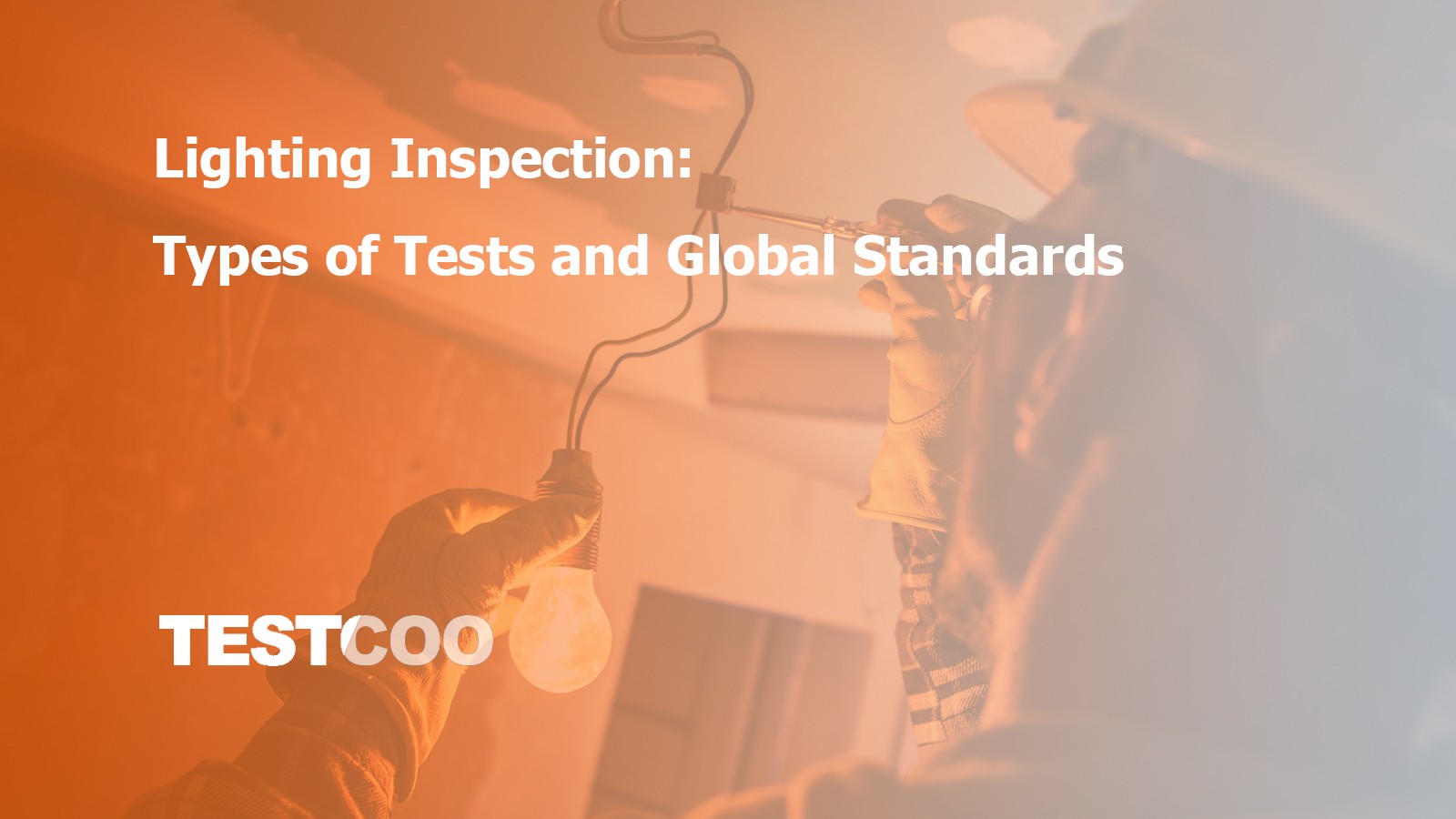
What Is Lighting Inspection?
Lighting inspection refers to the process of evaluating lighting products, such as LED bulbs, fluorescent lamps, luminaires and lighting fixtures, for their quality, safety, energy efficiency and compliance with relevant international or local standards. These inspections are typically carried out during different stages of the manufacturing process (pre-production, during production and pre-shipment) and also in laboratories for certification purposes.
The objective of lighting inspection is to ensure that the product:
- Works as intended
- Meets energy efficiency targets
- Is safe for use
- Complies with relevant regulations
- Will satisfy customer expectations
Why Is Lighting Inspection Important?
- Safety Compliance: Poorly manufactured lighting products can be a fire hazard or cause electric shock.
- Energy Efficiency: Lighting contributes significantly to energy use in homes and commercial buildings. Efficient lighting reduces utility bills and carbon footprints.
- Market Access: Products that fail to meet international standards may be barred from entering certain countries or regions.
- Customer Satisfaction: Substandard lighting can lead to complaints, returns and damage to brand reputation.
Types of Lighting Products That Undergo Inspection
- LED bulbs and tubes
- Compact Fluorescent Lamps (CFLs)
- Incandescent bulbs
- Halogen lamps
- Luminaires (including ceiling lights, downlights, panel lights, etc.)
- Outdoor and street lighting
- Automotive lighting
- Industrial lighting (e.g., high bay lights, floodlights)
Read more about Amazon Electronics Requirements for Sellers for Lighting Products
Types of Tests Performed During Lighting Inspection
Lighting inspections typically involve a combination of visual, mechanical, electrical, photometric and environmental testing. Below are some of the most common types of tests:
1. Visual Inspection
A basic but important part of lighting inspection that includes:
- Checking for defects in the housing, lens or heat sink
- Inspecting finishing quality (painting, polishing, sealing)
- Verifying labeling, logos and barcodes
- Confirming model numbers and rating labels
2. Functionality Test
- Verifies whether the light turns on and off correctly
- Ensures all features (e.g., dimming, color temperature adjustment) function properly
- Checks for flickering or buzzing sounds
3. Electrical Safety Test
These tests are vital to ensure user safety and include:
- Hi-pot test (Dielectric strength test): Measures insulation between live parts and accessible surfaces.
- Earth continuity test: Ensures proper grounding in metal-bodied products.
- Leakage current test: Verifies that electrical leakage is within safe limits.
- Power consumption test: Measures wattage to confirm energy use aligns with product claims.
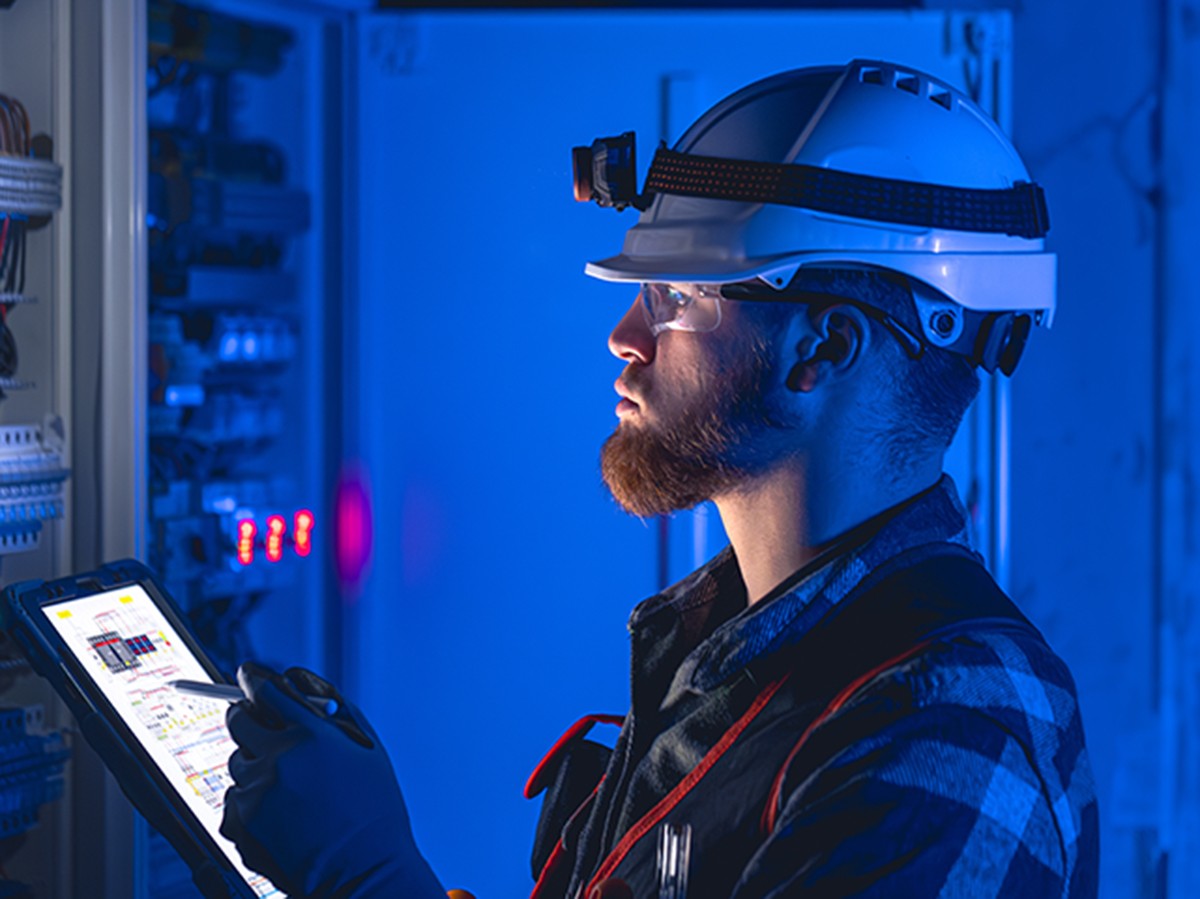
4. Photometric Test
- Luminous flux: Measures total light output in lumens.
- Luminous efficacy: Evaluates how efficiently the light source converts electricity into light.
- Color Rendering Index (CRI): Assesses how accurately colors appear under the light.
- Correlated Color Temperature (CCT): Determines if the light has a warm (e.g., 2700K) or cool (e.g., 6500K) hue.
- Beam angle: Important for task or directional lighting applications.
5. Thermal Test
- Temperature rise test: Ensures that the lighting fixture does not exceed safe temperature limits during use.
- Thermal management: Evaluates heat dissipation capabilities, especially critical for LEDs.
6. Mechanical Test
- Drop test: Assesses durability during transportation.
- Vibration test: Especially important for automotive or outdoor lighting.
- Torque test: Checks the strength and reliability of screw fittings.
7. Ingress Protection (IP) Test
- Evaluates the product’s resistance to dust and water.
- IP ratings like IP65, IP67 are especially important for outdoor lighting.
8. EMC/EMI Test (Electromagnetic Compatibility/Interference)
- Ensures the lighting product does not interfere with or is not affected by other electronic devices.
- Required by most markets for compliance.
9. Endurance and Lifespan Testing
- Simulates long-term use to verify manufacturer claims.
- Typically involves operating the product for thousands of hours.
10. Material & Component Verification
- Confirms the use of certified or approved components (e.g., drivers, LEDs, cables).
- Ensures flame-retardant and RoHS-compliant materials are used.
Read more about the Solar Light Inspection Service
Global Lighting Standards and Regulations
Different markets have their own set of lighting standards and regulatory requirements. Here’s a summary of key standards across major regions:
1. United States
- UL (Underwriters Laboratories): Safety standard for electrical devices.
- FCC Part 15: EMC compliance for electronic devices.
- Energy Star: Efficiency certification for residential and commercial lighting.
- IESNA LM-79 / LM-80: Testing standards for LED performance and lifetime.
2. European Union
- CE Marking: Mandatory for most electrical goods.
- EN/IEC 60598: Safety standard for luminaires.
- ErP Directive: Energy-related Products Directive requires efficiency labeling.
- RoHS Directive: Restriction of hazardous substances in electrical equipment.
- REACH: Addresses chemical safety.
3. China
- CCC (China Compulsory Certification): Mandatory for products entering the Chinese market.
- GB Standards: National standards governing product safety and performance.
- CQC Mark: Voluntary certification indicating quality.
4. Japan
- PSE Mark (Product Safety Electrical Appliance & Material): Required for most electrical devices sold in Japan.
- JIS Standards: Japanese Industrial Standards covering safety and performance.
5. Australia/New Zealand
- RCM (Regulatory Compliance Mark): Required for electrical safety and EMC.
- MEPS (Minimum Energy Performance Standards): Mandatory for energy efficiency.
6. Middle East
- SASO (Saudi Arabia): Lighting products require SASO quality mark and energy efficiency labeling.
- G Mark (Gulf Conformity Mark): Mandatory for electrical products sold in the Gulf Cooperation Council (GCC) countries.
7. India
- BIS (Bureau of Indian Standards): IS 10322 and IS 16101 are relevant lighting standards.
- BEE Star Rating: Indicates energy efficiency.
Challenges in Lighting Inspection
1. Constantly Evolving Standards
Regulatory changes require continuous updates in testing protocols and compliance strategies.
2. Variety in Product Types
From streetlights to smart lighting systems, inspection methods need to adapt to product complexity.
3. Global Supply Chains
Products are often designed in one country, manufactured in another and sold globally, each with different requirements.
4. Cost vs. Quality Balance
Brands are under pressure to reduce costs, which can affect material choices and quality assurance.
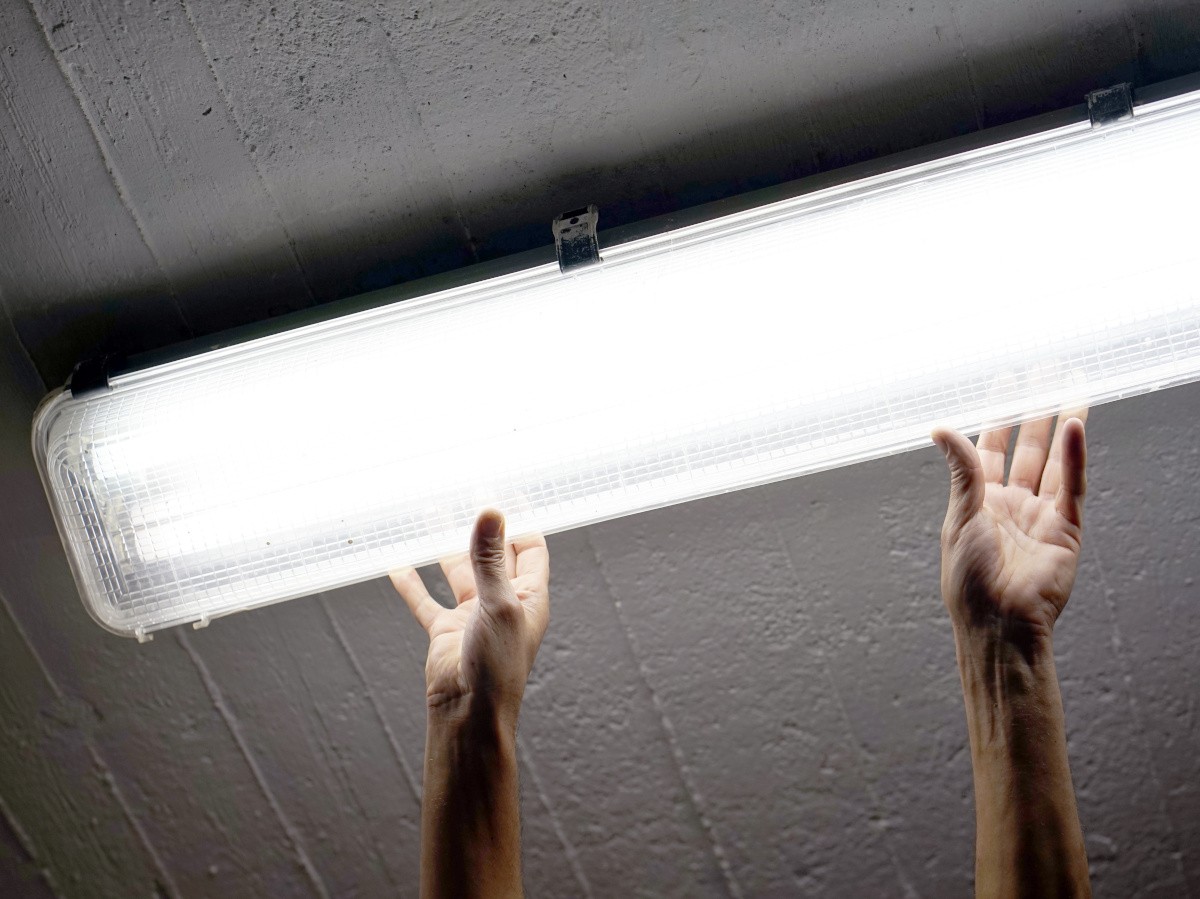
The Role of Third-Party Inspection Companies
Engaging a professional third-party inspection company helps mitigate the risks associated with substandard lighting products. Services offered include:
- Initial-production checks (IPC) - An Initial Production Check (IPC) is performed at the stage of about 10%-30% products finished for quality control inspection. It is the first step in ensuring the quality of your product will be consistent throughout production
- During production inspections (DUPRO) - During Production Check (DUPRO) is an essential preventative measure taken in the early stages of production, which can mitigate costly mistakes in the long run by highlighting any problems before too many defective items are produced and avoid affecting the shipping schedule
- Final Random inspections (FRI) - Final Random inspections (FRI) inspections act as a final check to evaluate product quality, packaging, product labeling and carton markings and ensure that items are correctly packed and fit for their intended use. The FRI takes place at 100% production completed with a minimum of 80% of goods packed and seated in shipping cartons for verification of your purchase specifications
- Factory audits and supplier verification - A factory audit is the assessment for production capability and performance of a factory against proven quality principles. Every production site needs reliable manufacturing and quality control systems to ensure customers are satisfied with their products
- Lab testing and certification - Lab testing is the scientific evaluation of a product to verify safety, performance and compliance with standards. Certification is the official confirmation by a third party that a product meets regulatory or industry requirements.
These services ensure that lighting products meet customer requirements and comply with relevant international standards before they are shipped.
FAQs
Q1. What’s the difference between LM-79 and LM-80?
A: LM-79 measures LED performance (light output, efficacy, etc.) under specific conditions. LM-80 measures lumen maintenance over time (i.e., how long the LED retains its brightness).
Q2. Can a product be certified for multiple countries at once?
A: Some certifications (like CB Scheme) help in obtaining multiple national certifications, but usually, individual approvals are needed for different markets.
Q3. How long does a lighting inspection take?
A: A pre-shipment inspection for a typical lighting order takes 1–2 days, while laboratory tests may take 1–4 weeks depending on the tests required.
Testcoo can help you with Third Party Lighting Inspections
Lighting inspection is an essential quality control measure in today’s competitive and highly regulated market. Whether you're a lighting manufacturer, retailer, importer or brand owner, understanding the inspection process and applicable global standards is crucial for product success. Integrate a robust lighting inspection process by partnering with Testcoo. We help companies keeping their customers safe. If you’re in the lighting business and need support with quality inspections, compliance or lab testing, contact us to can simplify your journey and help you shine in your market.
Free Sample Report Performance Quality Control
Download a sample report to keep control of your supply chain!
Featured Articles
- AQL Table | How to Read It
- TOP 10 Common Defects in Garments Quality Inspection
- Product Packaging and Shipment Label requirements for Amazon FBA
- What Is ASTM-F2413-18? Protective Footwear Standard
- How to Conduct Third-Party Quality Control Inspections for Electric Scooters
- SMETA Audit-What is SMETA Audit?
- TESTCOO Supplier Verification/Certification Service SLCP, Higg FEM, GRS, GOTS
- Quality Control Inspection Company in China
- What is Quality Inspection? A Complete Guide
- Guidelines for Product Inspection in India
Category
- Production Inspection Service
- Factory Audit
- Softline Inspection
- Hardline Inspection
- Electrics Inspection
- Certification
- Checklist
- Manufacturers
- Quality Assurance Basics
- Products Recall
- AQL
- Guidence and Standard
- News
- Supplier Management
- Amazon
- Protective Equipment
- e-commerce quality control
- Indian Manufacturing
- Soft Goods Quality Control
- Supply Chain Management
- Supply Chain Resilience
- E-Commerce Quality Control
- ISO 2859
- Supply Chain Optimization
- Garment Industry
- Higg Index