Compliance and Audit in Vietnam: APSCA, SLCP, SEDEX, Higg Index, GRS
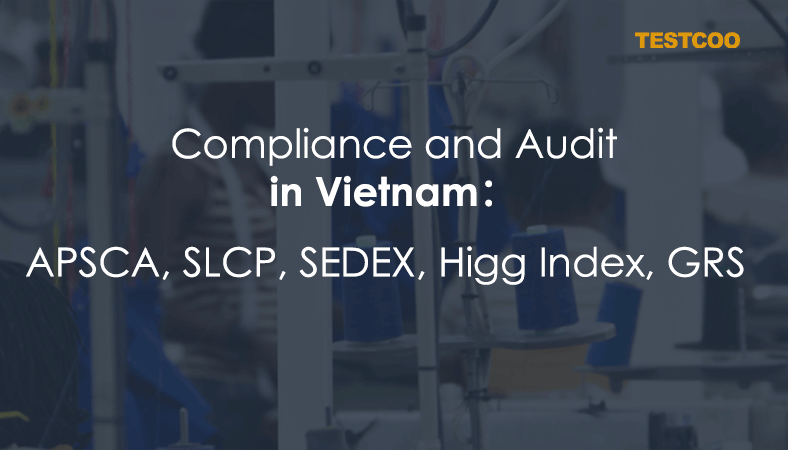
There are many risks associated with importing from Vietnam. Unqualified suppliers can subject your supply chain to a variety of disruptions, from factory disasters and negative publicity to legal repercussions and quality issues.
Factory audits, just like quality control inspections, remain an undervalued tool among importers to evaluate suppliers and minimize their risk when sourcing in Vietnam.
While audits often come at an upfront cost, the long-term value they provide can be tremendous. Factory audits can help you verify the legitimacy, trustworthiness and reliability of your suppliers to limit risk in your supply chain.
In this article, we discuss different types of the compliance and audit for importers to conduct that buying from Vietnam to help ensure the safety of supply chain.
Chapter 1: What is Compliance and Audit in Vietnam?
In recent years, a significant amount of manufacturing and supply chains shifting to Vietnam. When considering new suppliers, it is vital to vet them thoroughly and ensure they are the right fit for you as a buyer.
What is Compliance and Audit in Vietnam?
Compliance and audit are onsite inspections that can be done by the potential investor or a third party at a factory. A supplier audit allows you to assess a manufacturer and discover several issues, including unsafe working conditions, forced overtime, verbal abuse as well as health and safety issues.
A compliance and audit typically takes place after a group of potential suppliers have been screened to make way for the final few candidates. This audit is usually the last step in a sourcing process and is used to verify where goods are actually made as well as factory production capacity and capability.
Audits can also be used to ensure ongoing adherence to your requirements and assist you in supplier development. There are various types of audits in which assess your manufacturer’s quality management, environmental impact, social responsibility, or anything else that is important to your business.
Why do compliance and audit in Vietnam?
Many importers and brands diversifying their supply chains are choosing Vietnam to manufacture and export their products. However, these supply chain shifts can bring new challenges to a business, including labor problems, poor factory conditions, and environmental issue.
This is especially true for brands that manufacture in Vietnam and export their products using unreliable suppliers or factories. It is imperative for businesses to evaluate suppliers to prevent any supply chain issues that may affect business as normal.
Different types of audits can serve different purposes. They can help you:
Ensure compliance with retailer requirements
Ensure compliance with international labor and environmental laws
Evaluate your supplier’s quality management system and production capabilities
Chapter 2: 5 Types of Vietnam Factory Audits and Compliance
There is significant variance in what a factory audit covers and how businesses can approach the process.
The most common types of audits are social compliance audits, quality system audits, goods manufacturing audits, as well as an environmental audit. In addition to these, there are several sub-audits, such as the SA8000 and the SMETA audits, which are a form of social compliance audits. Check Selecting the right social compliance standard:Amfori: BSCI, SA8000, SEDEX SMETA, RBA, WRAP to learn more.
This article will introduce most 5 common types of compliance and audit to you: APSCA, SLCP, SEDEX, Higg Index, GRS. You can hire us to conduct several types of audits, depending on your needs as a company.
1. APSCA- Association of Professional Social Compliance Auditors
Founded in 2015, APSCA (the Association of Professional Social Compliance Auditors) is an industry association, whose members represent a substantial majority of the social compliance audit industry.
APSCA was created to help ensure the professionalism, consistency and credibility of individual auditors and organizations performing independent social compliance audits, and to promote the use of independent social compliance audits, as a tool to advance workplace conditions for workers globally.
As a practitioner-led initiative, APSCA was founded by leading social compliance audit firms including Arche Advisors, Bureau Veritas, ELEVATE, Intertek, SGS, RINA, TUV Rheinland, TUV SUD and UL.
The APSCA certification process will help ensure auditors have consistent training, education, background checks, and demonstrated competencies that are standard requirements in comparable professional auditor associations.
APSCA currently offers two types of membership for audit firms and individual auditors; respectively, Firm Membership and Auditor Membership.
APSCA’s Competency Framework includes the following topics:
- -Strategic and Systems Thinking
- -Professional and Ethical Behavior
- -Observation and Investigation
- -Data Collection and Analysis
- -Problem Solving and Analytical Decision Making
- -Management Systems
- -Documentation Review
- -Interview Skills
- -Communication, Relationship Management and Conflict Resolution
- -Self-Management
- -Standards, Laws and Regulations
- -Business Legitimacy and Integrity of Records
- -Underage Labour
- -Discrimination and Disciplinary Practices
- -Forced Labour
- -Working Hours and Overtime
- -Freedom of Association and Effective Recognition of the Right to Collective Bargaining
- -Harassment and Abuse Practices
- -Wages, Benefits and Terms of Employment
- -Subcontracting
- -Occupational Health and Safety
Check APSCA’s Competency Framework: APSCA-Competency-Framework-D-011-ENG
The apparel and footwear industry has traditionally been required to undergo costly, time-consuming and repetitive social audits to meet varying regulations and standards. The Social and Labor Convergence Program (SLCP) is a non-profit initiative established to provide a systematic assessment and verification process for stakeholders throughout global value chains.
What does SLCP do?
SLCP has brought together diverse stakeholders to create and implement a common tool to reduce the time and money spent on social auditing. The aim of SLCP is to redirect savings from auditing to improving working conditions. SLCP, through the Converged Assessment Framework, enables manufacturers to take ownership of their own social and labor data. SLCP provides a single comparable data set and facilitates collaboration between stakeholders.
The processes involved in SLCP Verification
In a nutshell, there are 3 stages, namely Data Collection, Verification and Data Sharing, and I'll be illustrating briefly them as below:
Stage 1 - Data Collection is handled by the facility. In most cases, the facilities are factories. As its name suggests, during the Data Collection stage, the facility has to fill in data being requested in either Excel format or with the online tools. It is important to note that even with Excel completion, the file will still be uploaded to the platforms for processing.
Stage 2 - Verification happens when the facility selects a Verifier Body to verify the data when it is ready. A Verifier will then be sent by the selected Verifier Body to have an on-site verification of data. Once the site verification is done, verification report will be submitted to platforms and the facility will have 14 calendar days to accept or raise disputes to the verification report. It will naturally proceed to the next step if the report is accepted, but if disputed, it will be ruled by SLCP’s Verification Oversight Organization.
Stage 3 - Data Sharing takes place once the verification report is finalised. Data is stored within the platforms but data ownership is with the facility. It’s entirely the facility’s decision to share the data with other parties, be they existing or new business partners.
Brands, retailers and organizations that accept SLCP verified data
Find more: https://slconvergence.org/slcp-data-acceptance
Manufacturers using SLCP
There is a list of manufacturers that have implemented or are actively planning to implement SLCP in their facilities.
Find more: https://slcpgateway.sustainabilitymap.org/facilities
Our experts in Vietnam are on-site to review your corporate social responsibility and the effectiveness of its implementation and help you ensure reliable social compliance and impact assessments of both the social and labor aspects of your facility.
Assess responsible business practices in your global supply chain with Social & Labor Convergence Program (SLCP) verification from Testcoo.
3. SEDEX
Supplier Ethical Data Exchange (Sedex) is a non-profit membership organization dedicated to improving ethical business practices in global supply chains.
Sedex’s factory audit standard is known as the SMETA (Sedex Members Ethical Trade Audit). SMETA is one of the most common factory audit standards in the world—Sedex currently boasts over 74,000 members, which helps you to understand standards of labor, health and safety, environmental performance, and ethics within your own operations or at a supplier site.
SEDEX also has its own online platform, in which importers can access official audit reports and view progress on corrective actions. And auditors can upload any kind of social audit on the platform, including SA8000 audits.
All the companies in any location can apply for the membership. SEDEX has won the favor of many large retailers and manufacturers. Many retailers, supermarkets, brand owners, suppliers and other organizations will ask cooperated farms, factories and manufactures to perform SMETA in order to be in line with the requirements of relevant ethical standards. Audit results can be recognized and shared by SEDEX membership. Thus, suppliers accept to conduct SEDEX inspection, which can avoid a lot of repeated audits from customers.
Overview of the SMETA audit
There are two types of SMETA audits to choose from:
The 2-pillar format covers
- Working practices and standards
- Health and safety
The 4-pillar format additionally covers
- Environmental audit
- Business ethics
Verification to SMETA only testifies to the degree to which the audited organization fulfills the requirements.
The SMETA audit process
Prior to your on-site audit, you should receive and complete a pre-audit information pack that contains a Self-Assessment Questionnaire (SAQ) and all the relevant details for conducting an efficient audit.
- -Opening meeting
- -Site tour
- -Interviews
- -Review of Records
- -Closing meeting
Importers with no experience with social compliance might find the SMETA report harder to interpret. You might consider starting off with a simpler framework like SA8000. Then, if needed, you could consider a SMETA audit once you have a stronger grasp on your supplier’s compliance.
4. Higg Index
↵
The Higg Index is a suite of tools for the standardized measurement of value chain sustainability, and it is central to the SAC’s mission to transform businesses for exponential impact.
To enable systemic change, companies and organizations need a common language and platform in order to track and measure their social and environmental impacts. The Higg Index provides this language, empowering brands, retailers and manufacturers to leverage verified data in order to measure, improve and share their performance.
The methodologies of the Higg Index were developed over the course of ten years in partnership with SAC members, consultants, stakeholders, and industry experts and are continuously evolving based on the latest scientific research and data. Today, more than 21,000 organizations around the world are using the Higg Index, and its global reach and variety ensure that the SAC can now catalyze change from within the industry. Since its launch in 2011, it has become the leading environmental and social assessment in the apparel industry, which measures the whole value chain at this scale.
Over the last decade, the SAC together with its members have gathered a wealth of verified data. With this data, the industry can identify hotspots, continuously improve sustainability performance, and achieve the environmental and social transparency consumers are demanding.
Across topics such as water use, carbon emissions, and labor conditions, consumer goods brands, retailers, manufacturers, governments, NGOs, and consumers can use the Higg Index to inform their individual sustainability strategies and drive collective industry transformation.
Consumer goods production takes place at thousands of facilities around the world. Each facility plays a key role in the overall sustainability of the industry. The Higg Facility Tools offer standardized social and environmental assessments that facilitate conversations among value chain partners to socially and environmentally improve every tier in the global value chain.
Higg Facility Tools
The Higg Facility Tools measure an individual factory’s social and environmental performance. The tools are made up of two modules:
1. Higg Facility Environmental Module (Higg FEM)
The Higg Facility Environmental Module (Higg FEM) informs manufacturers, brands, and retailers about the environmental performance of their individual facilities, empowering them to scale sustainability improvements.
The Higg FEM provides facilities a clear picture of their environmental impacts. It helps them identify and prioritize opportunities for performance improvements. The Facility Environmental Module measures:
Environmental management systems
- -Energy use and greenhouse gas emissions
- -Water use
- -Wastewater
- -Emissions to air (if applicable)
- -Waste management
- -Chemical use and management
2. Higg Facility Social & Labor Module (Higg FSLM)
The Higg FSLM assesses the social and labor conditions present in a facility and the effectiveness of social management programs. Instead of focusing on compliance, they can dedicate time and resources to making lasting systemic changes. The Facility Social & Labor Module measures:
- -Recruitment and hiring
- -Working hours
- -Wages and benefits
- -Employee treatment
- -Employee involvement
- -Health and safety
- -Termination
- -Management systems
- -Facility workforce standards and those of value chain partners
- -External engagement on social and labor issues with other facilities or organizations
- -Community engagement
5. GRS
The Global Recycled Standard (GRS) is a full product standard to verify and track recycled raw materials through the supply chain. It also includes processing criteria to prevent the use of potentially hazardous chemicals, and verifies positive social or environmental production at the facilities.
GRS has been one of the widely recognized certification program in the textile industry now. The primary goal of the GRS is to increase use of recycled materials in products and reduce the harmful social, environmental, and chemical impacts of production.
The objectives of the GRS
The Global Recycled Standard is intended for use with any product that contains at least 20% Recycled Material. Each stage of production is required to be certified, beginning at the recycling stage and ending at the last seller in the final business-to-business transaction.
Material Collection and Material Concentration sites are subject to self-declaration, document collection, and on-site visits. The GRS does not address quality or legal compliance.
Social Requirements
Workers employed at facilities involved in the production of GRS products are protected by strong social responsibility policy.
01 Forced, bonded, indentured and prison labor
02 Child Labor
03 Freedom of association and effective recognition of the right to collective bargaining
04 Discrimination, harassment and abuse
05 Health and safety
06 Wages, benefits and terms of employment
07 Working Hours
Environmental Requirements
Facilities involved in the production of GRS products have strong environmental protections in place.
01 Energy use
2 Water use
3 Wastewater / Effluent
4 Emissions to Air
5 Waste management
Chemical Requirements
Chemicals used in the production of GRS products do not introduce unnecessary harm to the environment or workers.
1 Inherently problematic substances
2 Exclusion of substances and mixtures classified with particular hazard codes or risk phrases
Learn more: Global-Recycled-Standard-v4.0
How to Get Certified
The GRS label applies to companies in the textile sector with activity in spinning knitting, printing, stitching, ginning, weaving and dyeing, but also to recyclers, distributors and brands who want to have their recycled products and their responsible practices recognized by an international label.
Chapter 3: How Testcoo can Help Vietnam Compliance and Audit?
Global demand for textile and apparel is growing along with this shift in sourcing opportunities. Vietnam has proven to be capable of producing labor-intensive products, including textiles and apparel, at a lower cost. However, supply chain shifts can bring new challenges such as poor labor and factory conditions as well as product quality issues.
Importers looking to manufacture in Vietnam should carry out a thorough audit of their suppliers to ensure their network is protected from risks and quality issues. Businesses should seek to identify independent advisors with an in-country presence to audit suppliers in Vietnam.
TESTCOO third-party compliance and audits in general can help organizations to identify critical issues in their business practices and empower them to mitigate and manage supply chain risks.
Chapter 4: FAQs about Compliance and Audit in Vietnam
1. When might I need a SMETA audit?
If you are part of a retailer/brand’s supply chain, they may request that you have a SMETA audit conducted at your site. However, the SMETA audit can also be requested directly by the site without client or brand involvement. This allows sites to proactively improve standards within their business.
2. How is SLCP different from other audit programmes/standards such as amfori and SMETA?
The purpose of SLCP is to remove audit fatigue and so, instead of being another set of different requirements, the CAF has taken 21 other common audit programmes and standards into consideration already. In other words, by conducting SLCP verification, facilities would have fulfilled most of the information needed by other major standards. According to SLCP, CAF satisfies 97% of the information required if CAF is fully completed.
Another key difference is that SLCP Verification does not provide scoring. Upon finishing the verification, the facilities will not get a Pass/Fail result or Corrective Action Plans (CAPs) like they normally do in other audit programmes/standards. Interpretation of the validated data lies on the users whom facilities share the report with.
3. Why is SLCP needed?
Most stakeholders in our industry now agree: while the traditional approach to auditing has played a significant role in improving social and labor conditions over the past two decades, it has also led to a proliferation of different standards, codes and protocols, and in turn to a proliferation of audits. There is broad recognition that audits alone do not create systemic change. We have much further to go to create sustainable remediation. SLCP’s Converged Assessment Framework (CAF) will free up resources currently tied up in auditing and promote collaboration that will make tangible and lasting improvements to working conditions and workers’ lives.
Conclusion
Vietnam has engaged with the international business community and opened its doors to investors worldwide. As a result, Vietnam has become an attractive alternative to China for production.
To properly analyze your suppliers and ensure the factory operates at the highest standards, you can hire an inspection company that will audit your factory and verifies that the supplier is who they claim they are.
Take a close look at the requirements of the retailers and markets you sell to, your customers’ expectations and your supplier relationships. Could an audit help improve transparency into your supplier’s operations and reduce risk in your supply chain? For many importers, the answer to that question is “yes”. Auditing is a must-have for every business starting production in Vietnam.
Testcoo has a team of social compliance certified auditors that can assist in auditing your suppliers against your own or international audit standards, and which can aid suppliers to resolve quality issues through corrective action.
Our range of compliance and audit in Vietnam includes:
APSCA
SLCP
SEDEX
Higg Index
Free Sample Report Performance Quality Control
Download a sample report to keep control of your supply chain!
Featured Articles
- AQL Table | How to Read It
- TOP 10 Common Defects in Garments Quality Inspection
- Product Packaging and Shipment Label requirements for Amazon FBA
- What Is ASTM-F2413-18? Protective Footwear Standard
- How to Conduct Third-Party Quality Control Inspections for Electric Scooters
- SMETA Audit-What is SMETA Audit?
- TESTCOO Supplier Verification/Certification Service SLCP, Higg FEM, GRS, GOTS
- Quality Control Inspection Company in China
- What is Quality Inspection? A Complete Guide
- Guidelines for Product Inspection in India
Category
- Production Inspection Service
- Factory Audit
- Softline Inspection
- Hardline Inspection
- Electrics Inspection
- Certification
- Checklist
- Manufacturers
- Quality Assurance Basics
- Products Recall
- AQL
- Guidence and Standard
- News
- Supplier Management
- Amazon
- Protective Equipment
- e-commerce quality control
- Indian Manufacturing
- Soft Goods Quality Control
- Supply Chain Management
- Supply Chain Resilience
- E-Commerce Quality Control
- ISO 2859
- Supply Chain Optimization
- Garment Industry
- Higg Index