装运前检验质量管控要点:十大风险点解析与预防策略
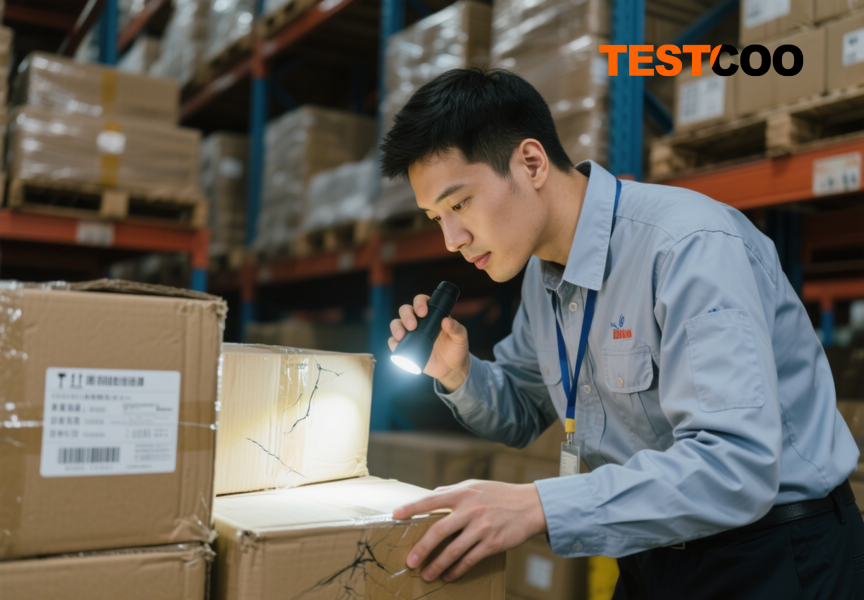
装运前检验(PSI)作为供应链质量管控的关键环节,承担着确保产品符合质量标准、法规要求及客户预期的重要职责。然而,在实际操作中,一系列潜在陷阱可能导致检验效能折损,甚至引发质量风险、合规隐患与客户信任危机。本文系统梳理十大典型陷阱,并提供结构化解决方案,助力企业构建严谨高效的检验体系。
1.准备不充分
陷阱解析
检验前的信息缺失可能引发连锁反应:对产品技术参数(如材质等级、性能指标)理解模糊,会导致现场检验无据可依;未明确抽样比例与测试标准,可能使检验结论缺乏统计学效力;忽略客户特殊要求(如包装颜色代码、标签语言版本),易造成交付后合规争议。此类准备漏洞本质上是检验目标与执行路径的脱节,直接影响检验的针对性与有效性。
系统应对
建立三层准备机制:
- 文件预审:提前72小时完成采购合同、技术图纸、行业标准(如ASTM、ISO)的交叉核对,标注关键验收条款(如AQL允收水准);
- 场景模拟:针对复杂产品(如机电设备),制作检验流程图,标注必检点(如安全保护装置联动测试);
- 资源调配:根据产品特性预配专用工具(如卡尺、绝缘测试仪),确保现场操作的连贯性。
2.检验人员培训不足
风险本质
检验人员的专业能力是质量把控的核心变量。缺乏工艺知识(如注塑件的缩水率判断)会导致外观缺陷漏检;不熟悉新兴标准(如REACH法规对SVHC物质的限值)可能使有害物质残留问题被忽视;操作手法不规范(如硬度计压针停留时间不足)则会造成数据偏差。此类问题反映出培训体系与行业发展的脱节。
能力建设路径
实施动态培训矩阵:
- 基础层:新入职人员需通过学习培训,涵盖抽样原理、缺陷分类(致命/重/轻缺陷)等核心知识;
- 提升层:每季度开展专项培训(如新能源产品的电池安全检验),结合案例分析强化场景应用能力;
- 评估层:建立“理论考核+实操演练”双轨认证机制,不合格者需复训直至达标。
3.检验方法不一致
隐性危害
非标准化操作会引发质量控制的“薛定谔效应”:同一批次产品经不同检验员判定可能得出迥异结论,导致供应商整改方向混乱;模糊的判定标准(如“表面光洁度良好”)易引发争议,削弱检验公信力;随意调整检验顺序(如先包装后功能测试)可能掩盖装配缺陷,形成质量隐患。
标准化实施框架
构建全流程操作指南:
- 程序文件:制定《检验作业指导书》,细化至每个检验步骤的耗时、工具型号、判定依据(如GB/T2828.1抽样标准);
- 视觉基准:建立缺陷样本库(如划痕长度≥2mm为不合格),配套高清图示供现场对照;
- 数据校准:每周对检验设备进行精度校验,确保量值传递的准确性。
4.样本量不足
统计学谬误
过小的样本量可能使检验陷入“以偏概全”的陷阱:对于万件级批量,仅抽检5件可能漏检3%的缺陷率;未考虑产品分层(如生产线早班与夜班的工艺波动),会导致样本缺乏代表性;凭经验而非科学方法确定样本量,易使检验沦为“形式主义”。
科学抽样策略
应用分层抽样模型:
- 基数分层:根据批量大小执行不同抽样方案;
- 风险加权:对关键特性(如电器产品的绝缘耐压)实施加严抽样,样本量提升30%;
- 动态调整:根据供应商历史质量表现(如连续3批合格则转为放宽检验),实施抽样方案动态切换。
5.忽视包装和标签
全链条影响
包装防护不足可能使合格产品在运输中变为“不良品”:瓦楞纸箱克重不达标导致挤压变形,缓冲材料选型错误引发部件断裂;标签错误(如成分标识缺失、条形码扫描失败)可能触发海关扣留、零售商罚款等连锁反应,直接影响品牌声誉。
防护性检验要点
建立包装可靠性验证体系:
- 结构检验:核查包装设计文件(如堆码层数、抗跌落高度),模拟运输环境(如振动测试、冲击试验);
- 标签合规性:对照目标市场法规(如欧盟CE标签的语言要求、美国FCC认证标识),逐项核验内容完整性;
- 实操测试:随机抽取3件包装件进行模拟装卸测试,验证封箱强度与标识耐久性。
6.忽视环境和社会合规性
ESG风险传导
合规性缺失的后果具有滞后性与放大效应:供应商违规使用童工可能在产品上市后引发舆论危机;生产过程废水排放超标可能导致供应链被列入环保黑名单;未履行碳足迹申报义务可能错失国际客户订单。此类问题反映出检验视角的局限性——从“产品质量”到“企业责任”的维度拓展迫在眉睫。
合规性嵌入方案
构建供应链ESG审计模块:
- 前置审核:要求供应商提供ISO14001环境管理体系、SA8000社会责任管理体系认证文件;
- 现场核查:检验时同步抽查生产记录(如危废处理台账、员工工时考勤),确认合规措施落地;
- 动态监控:接入第三方数据平台(如EcoVadis评级),实时追踪供应商合规风险变化。
相关阅读:社会责任审核指南:构建道德供应链与企业 CSR 实践全解析
7.仅依赖目视检验
感官局限性
视觉检查的物理边界显著:电子产品的焊点虚焊、机械部件的内部裂纹、化工产品的成分偏差等隐蔽缺陷无法通过肉眼识别;对于需长期使用才能暴露的问题(如塑料件的耐老化性能),目视检验更是力有不逮。单一检验手段可能使“合格报告”成为质量盲区的遮羞布。
多维检验技术整合
实施全生命周期检验模型:
- 功能验证:对机电产品进行空载/负载运行测试,记录温升、噪音等关键参数;
- 精密检测:运用X射线探伤、光谱分析等技术手段,对隐蔽结构与成分进行定量分析;
- 模拟使用:针对消费品开展用户场景测试(如手机按键寿命试验),验证实际使用性能。
8.记录不充分
追溯性危机
检验记录的模糊性会导致质量问题“死无对证”:缺乏缺陷位置标注的报告无法指导供应商精准整改;遗漏环境参数(如检验时的温湿度)可能使异常数据归因失焦;手工记录的随意涂改会丧失证据效力,在纠纷中处于被动。本质上,这是对“检验即证据链构建”认知的缺失。
数字化记录体系
搭建检验数据管理平台:
- 结构化录入:使用预设模板记录检验时间、环境条件、样本编号、缺陷描述(如“PCB板C10位置焊盘脱落”);
- 多媒体存档:对不合格项拍摄多角度高清照片,关键部位标注尺寸数据;
- 权限管理:检验记录经双人复核后锁定,任何修改需留痕并附审批记录。
9.与供应商沟通不足
信息不对称成本
单向的检验指令传递会形成“质量黑洞”:供应商不了解客户的特殊验收标准(如汽车行业的PPAP要求),可能导致批量返工;检验结果反馈滞后(如一周后才通知问题)会延长整改周期,影响交付计划;缺乏整改指导会使供应商陷入“试错循环”,消耗双方资源。
协同式质量管控
建立双向沟通机制:
- 预检验沟通:检验前3天召开线上会议,明确本次检验的重点(如新增的环保要求);
- 实时反馈:现场发现重大问题时立即启动“检验-供应商-客户”三方会议,同步确认处置方案;
- 闭环管理:出具《不符合项报告》,明确整改期限(如7个工作日)、验证方式(如提交整改前后对比报告)。
10.跳过后续检验
质量改进断层
缺乏验证的整改等同于“未整改”:供应商可能采取临时补救措施(如更换表面缺陷部件而不优化工艺),导致问题反复发生;未跟踪整改效果会使检验体系丧失持续改进动力,陷入“发现问题-遗忘问题”的恶性循环。
闭环管理机制
设计PDCA改进回路:
- 计划阶段:在首次检验报告中明确需复验的项目(如前次不合格的焊接强度);
- 执行阶段:整改完成后,供应商需提前48小时申请复验,提交自检报告;
- 检查阶段:复验时重点核查历史问题对应的工艺环节(如焊接参数监控记录);
- 处理阶段:连续两次复验合格后,将该问题纳入年度审核重点,降低复发概率。
装运前检验的价值不仅在于“发现问题”,更在于通过系统性的流程设计阻断问题的产生与传递。企业需以“预防为主、全链管控”为理念,将检验从单一的质量把关环节升级为供应链协同改进的枢纽——通过精准的前期准备、专业的人员能力、科学的方法体系、透明的沟通机制,构建覆盖“策划-执行-验证-改进”的完整质量控制闭环。唯有如此,方能将检验陷阱转化为质量提升的契机,最终实现产品竞争力与客户满意度的双重跃升。
作为专业的质量管控解决方案提供者,TESTCOO始终致力于帮助企业构建严谨高效的装运前检验体系。我们依托标准化的检验流程、数字化的记录系统与全链条的合规管理能力,助力客户将检验陷阱转化为质量提升的契机,最终实现产品竞争力与客户满意度的双重跃升。选择TESTCOO,让每一次检验都成为品质信赖的起点,为全球供应链的可靠性筑牢根基。