防止产品出现质量缺陷的4个步骤
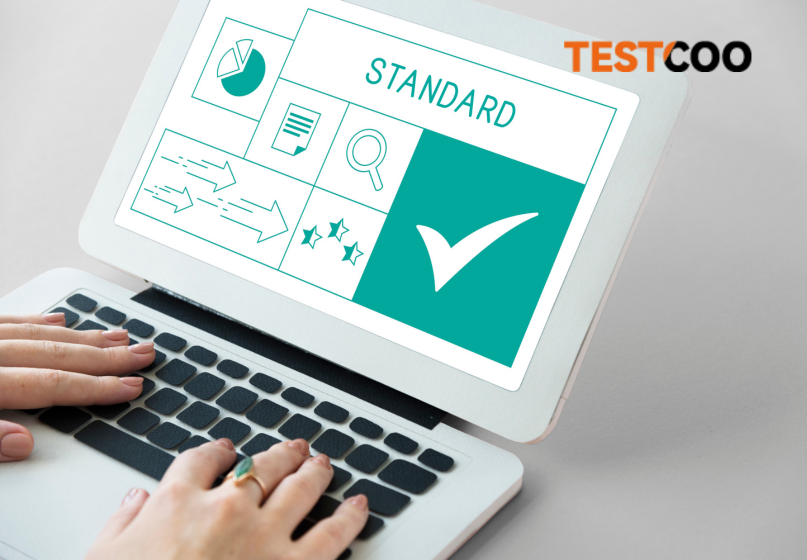
您在产品出现质量缺陷后,花费多少时间来查找和修复问题?
如果您与大多数贸易商一样,答案很可能是"比预期的更多"。在大规模生产后处理质量缺陷,往往会在临近出货截止日期时占用宝贵时间。订购替换材料或组件、生产替代单元、进行返工和重新检验,这些都可能在最紧迫的时刻延误发货。
许多贸易商依赖出货前检验来管控产品质量。但若您仅依靠检验来识别和解决产品中的质量缺陷,您已处于被动应对状态。 等到生产结束后才处理质量问题,通常意味着本可预防的缺陷已影响了订单中的大部分产品。
只需在生产前采取几项预防措施,贸易商往往就能显著减少货件中的质量缺陷数量。
让我们深入探讨预防质量缺陷的四个关键步骤及其如何帮助您有效管理产品质量。
1. 审核潜在供应商的质量管理体系
许多贸易商倾向于与持有ISO 9001-2015认证的供应商合作,因为他们认为这能为生产能力和质量控制流程提供一定保障。
但工厂拥有ISO 9001证书并不等同于真正落实了标准中的实践。例如,在亚洲部分地区,工厂可能通过宽松的认证机构或贿赂审核员获得认证。
质量审核(或称供应商评审)是对工厂质量管理体系(QMS)的系统性检查,通常以ISO 9001标准为基准。供应商实地审核可为您提供工厂的以下关键信息:
- 人员培训:检查员工培训是否涵盖与其岗位相关的特定缺陷教育
- 采购管理:核查评估和批准次级供应商的流程,以及设定生产投入的验收标准
- 生产与过程控制:审查作业指导书、工艺标准、生产设备、环境控制、清洁与污染防控措施
- 检验、测量与测试设备:确认工具设备的校准状态以确保测量结果精准
- 验收、标识与追溯活动:检查来料、在制品及成品质量控制的记录与执行程序
- 不合格品管控:核查缺陷产品的标记、识别、评估、隔离、处置和返工程序
- 标签、包装、搬运与储存:确保流程能防止产品混淆、损坏、变质或污染
- 质量记录、统计与分析:审查抽样方法、缺陷收集机制、纠正预防措施及客诉处理流程
质量审核如何帮助预防质量缺陷?
许多贸易商在选择供应商时,将质量审核作为资质认证流程的一部分。通过审核收集的信息可帮助您规避与无法满足生产标准的"不良供应商"合作的风险。
工厂的内部质量控制流程对管理来料和制程质量至关重要——这些环节通常超出您的直接管控范围。许多供应商早在客户介入其工厂质量管理前,就已从次级供应商处采购原材料和组件。
供应商审核可能揭示的"危险信号"包括:
- 缺乏正式的来料质量控制流程或次级供应商筛选机制
- 文件记录缺失:包括营业执照、QMS证书、内部审核报告、生产流程图、作业指导书及纠正预防措施报告
- 工人培训不足且无培训档案
但质量审核不仅限于供应商选择阶段——您可在进口业务的任何环节实施审核。若遭遇严重质量问题,审核还能揭示工厂生产或质检流程中的缺陷根源。
2. 谈判时根据质量目标设定合理价格
若未采用优质材料和部件,生产高质量产品几无可能。例如,再精良的衬衫设计也无法弥补劣质面料的缺陷;配置错误摄像头或显示屏的智能手机必然导致客户退货。
过度压价将严重危及成品质量。与多数贸易商类似,工厂管理者通常严格控制成本以确保盈利。
许多供应商会接受低价订单,但这几乎总以牺牲质量为代价,具体表现为:
- 使用低于约定标准的廉价原材料
- 用低成本替代品替换关键组件
- 赶工生产导致工人粗心,缺陷率飙升
这些问题往往到生产后质检时才暴露,此时预防缺陷为时已晚。您可能面临整批存在质量问题的滞销货物,不得不在发货前紧急处理。
如何在保证质量的前提下优化成本?
低价未必意味着必须妥协质量。以下获取最佳报价}的实践可助您平衡成本与质量:
- 多方比价:向多家供应商索取报价,了解产品市场均价并评估报价竞争力
- 要求提供物料清单(BoM)与分项报价:BoM详细列明终端产品所需的原材料和子组件
- 提供大宗原料采购预测:针对铝材、钢材或芯片等价格波动较大的原料,批量采购可降低单位成本
- 优化产品设计:简化生产工艺、减少组件数量可显著降低制造成本
3. 建立标准样品以明确质量预期
验证供应商实力的最佳方式是在量产前索要产品样品。制作样品要求工厂实际展现其达成质量标准的制造能力。
筛选供应商时,样品质量验证可帮助判断报价是否与实物质量匹配。即使已选定供应商,仍需持续要求并审核样品。样品是设定量产质量基准、预防缺陷的关键工具。
标准样品为您提供以下问题的前置解决机会:
- 原材料与部件的选用
- 产品规格符合性
- 功能与性能达标度
- 包装设计与品牌呈现
经您审核确认的样品即成为"黄金标准"。生产过程中,工人可参照该样品自主纠正偏差,防止缺陷波及整批货物。
如何审核标准样品?
多数情况下,您可自主审核样品:
- 对照规格书检查产品外观与尺寸
- 模拟实际使用场景测试功能
- 验证包装完整性与品牌标识
对需符合国际标准或法规的产品(如电子设备、儿童用品),建议送样至认证实验室进行:
- 安全性能测试
- 耐久性评估
- 材料成分分析
- 竞品对标测试
- 包装强度验证
若样品体积庞大(如家电、家具),可委托第三方检验机构在供应商现场或当地办事处审核,节省物流成本与时间。委托时需注意:
- 提供完整的产品规格与测试要求
- 审核后确保样品返还工厂并加贴防拆封标记
- 明确定义标准样品的参考效力,防止中途调换
4. 通过质量手册设定缺陷容忍度
标准样品不应是生产中的唯一参考。您应向供应商提供质量手册(或质检清单),作为工厂人员的主要执行依据。
部分贸易商仅通过邮件发送零散要求,而整合式的质检清单具有以下优势:
将技术要求、缺陷容忍度、检验流程等整合为3-10页的简明文档(复杂产品可达更长篇幅)
包含关键信息:
- 产品规格参数
- 质量缺陷接受标准
- 现场测试要求(如跌落测试、功能验证)
- 包装规范(运输包装与零售包装)
虽然优质工厂会自编质量手册,但这些文件往往针对多客户通用,可能忽略您的特殊要求。因此,务必在生产前将定制化质检清单发送给供应商,避免因理解偏差导致缺陷。
发送清单后需主动询问供应商是否存在疑问。由于文化差异,工厂人员可能不会主动提出困惑,需要您反复确认。
第三方检验公司如何协助制定质量手册?
若已委托第三方检验公司进行常规检验,其专业经验可助力清单优化:
现场测试设计:根据产品特性推荐适用的测试项目与设备
抽样方案制定:采用ANSI/ASQ Z1.4等统计抽样标准
缺陷分级规则:明确致命/主要/次要缺陷的判定标准与验货结论规则
需注意:制定清单时应与供应商充分沟通,确保其具备执行能力。但最终标准必须基于您对质量的要求——例如,标准样品的审核必须完整传递您的技术规范,避免第三方误解。
作为贸易商,您固然可通过出货前检验管控质量,但这仅能帮助发现问题而非预防问题。相较事后补救,通过上述措施防患于未然往往更高效经济。
但需谨记:预防措施与检验手段缺一不可。建议在生产完成80%-100%时仍进行生产终期检验,构建完整的质量控制体系。唯有预防与检验双管齐下,方能最大限度保障产品品质。